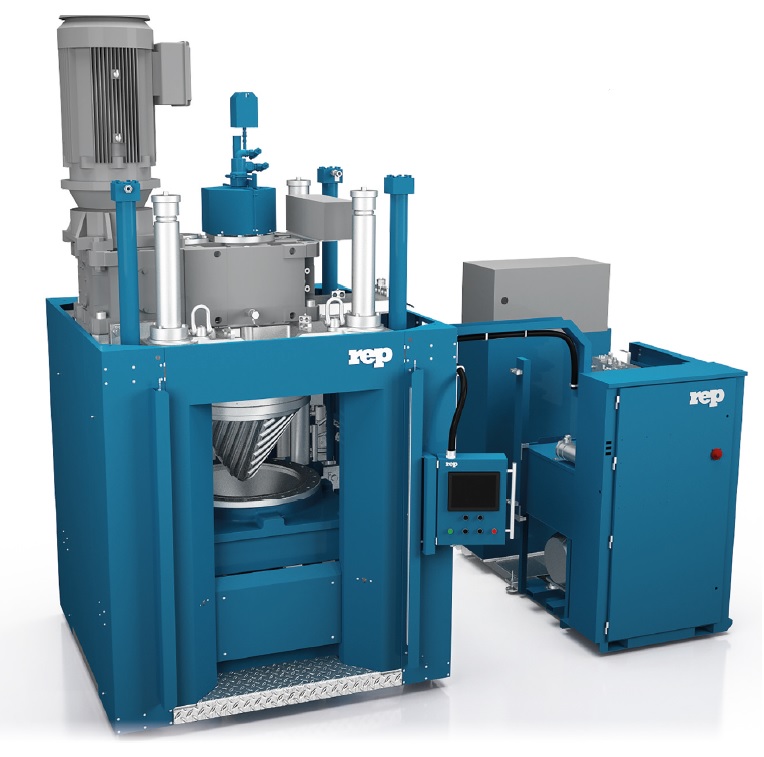
REP社が自社発行雑誌2022年3月号 Volume 17で発表したものです。
REP社は、1961年に世界で初めてゴム専用の射出成形機を世に送り出した、射出成形機専門メーカーです。
1965年の初号機から日々改良を重ね、最新の第10世代射出成形機は、人間工学に基づく確かな作りと
生産性を兼ね備えた装置となっております。
全世界へ累計10,000台以上の射出成形機を送り出し、ゴム用射出成形機のパイオニア、そして
トップメーカーとして日々進化を続けています。
目次
1 はじめに
今日ゴム廃棄物の処理と廃棄方法に関してはゴム業界における大きな挑戦の一つになってきています。マーケティングや環境意識によって、または新しいルールによってゴム製品製造各社はゴム廃棄物の削減方法とリサイクル方法を模索しています。
廃棄物は埋め立て地での処分、焼却処分、または熱分解で処理されるのが一般的で
ゴムのリサイクルというのは次に示すようにかなり複雑で困難なプロセスです。
ゴムが加硫される際、ゴムを構成するポリマーチェーンは加硫剤によって(主に硫黄)鎖状の様々な場所において図1のBで示すように科学的に結合していきます。これらの結合はクロスリンクとして知られており、加硫反応終了後にポリマーチェーンの3Dネットワークを構築します。このクロスリンクがゴム特有の機械特性を付与します。
理想的なゴムのリサイクルとしてはクロスリンクの破壊を破壊し、他の製品と混ぜて加硫ができるように脱硫を行う事です。しかしながら一度クロスリンクが形成されると、それを壊すことはとても難しいのです。
このことはゴム製品の日常生活における使用においては大きなメリットとなりますが、脱硫という面からみると一番の障害となります。
この課題の目的はREP Internationcal(以後REP)によって開発されたHigh Schear Mixing(以後HSM)と呼ばれる熱機械的脱硫プロセスでゴムを研究することです。
1.1 脱硫の原理
近年脱硫に関する仕事量が増加してきています。この脱硫のために様々な方法が考案されていますが、方法としては主に2つのカテゴリーにわけられます。
・ケミカルプロセス:クロスリンクを攻撃して破壊する目的で微生物や化学化合物を使用する方法
・物理プロセス:機械的、熱機械的、マイクロ波や超音波を使用する方法
ここで研究調査されているような物理的脱硫プロセスは加硫ゴムを形作る分子間の様々な結合エネルギーを利用することを目的にしています。
C-C結合はC-S結合よりも強固で、C-S結合はS-S結合よりも強固です。アイデアはS-S結合またはS-C結合のクロスリンクを破壊するためにエネルギーをあたえることで、ポリマーチェーンを形成するCーCを破壊するのではありません。
典型的な結合エネルギーはテーブル1に示す通りです。
これらすべてのプロセスは脱硫プロセスと呼ばれていますが、実際にはこれらの方法の結果はクロスリンクの切断と主鎖切断の組み合わせです。
図1C1は主鎖とクロスリンクのランダム切断と定義される再生化を描写しています。
図1C2はクロスリンクのみを切断したゴムの脱硫プロセスを示しています。
2 HSMプロセス
HSM処理はゴムにハイレベルなせん断と選択的にクロスリンクを破壊する効率的な方法をもたらす伸長ストレスをあたえることから成り立っています。
これは表面に何本もの溝が刻まれた2つの円錐型金属コーンによって行われます。(図2参照)金属コーン間の距離はギャップと呼ばれます。
この2つのコーンの間にゴムがセットされると、 ギャップ、回転速度、回転方向などのさまざまなパラメータ によりゴムが刻まれた溝に移動し、連続的にそして迅速な方法でストレスを加えたり緩和したりします。
最初のHSMプロセス分析は2018年に発表されました。その際はバッチ処理によって行われ、処理できる量は約2㎏(実験機)で数分間処理を行い、その後後工程(フィルタリグ)のために取り出していました。
今日では一連のプロセスは改良され、バッチシステムによる処理は必要ではありません。今は連続で処理が可能です。HSMの新しいバージョンの概要は図2をご参照ください。
HSMプロセスの最中、ゴムは自然に発熱していきます。ゴム温度が不必要に上がることを避けるため、金属コーンの熱を拡散させるために冷却システムが役に立ちます。図2でわかるように冷却システムは金属コーン内部に独立した2系統の経路を有しています。
温度センサーも複数個所に取り付けられており、温度は常に監視されています。
3 製法研究
以前の検証ではEPDMの結果について協議しましたが、今回の研究では3種類の異なったゴムを取り扱っています。エチレンアクリルエラストマー(AEM)、フロロエラストマー(FKM)、そして天然ゴム(NR)です。それぞれのゴムの製法に関してはテーブル2-4に記載しています。最初のサンプルは0%のHSMゴムです。すべての製法において3.5㎏製造しました。製法の調整はすべての場合においておこなっておりません。
AEMとNRは最初にニーダーにて練り合わせ、その後オープンミルにて促進しています。FKMは練から促進までオープンミルを使用しております。すべての混合において同じステップと時間を踏むように注意を払っております。
3.1 未加硫ゴムテスト
すべての未加硫ゴムはムニー粘度(ML(1+4):ISO289-1)とMDR(ISO6502)での加硫特性を検証しています。
3.2 加硫
すべてのサンプルシートは2mmに整えられ、プレスに加硫されました。すべてのサンプルの加硫時間はテーブル5に記載しております。AEMとFKMはゴムを形つくるための1次加硫に続き2次加硫を行うのが一般的です。2次加硫の影響を検証するため、2つのゴムの何点かは2次加硫を実施しました(テーブル2&3にてPVと表記)。AEMは175度で4時間、FKMは200℃で6時間。
3.3 加硫ゴムテスト
加硫済みゴムシートを使用して異なるテストを実施しました。
・引張応力/伸び特性の判断(ISO37)
・引裂き強度の判断(ISO34-1)
・硬さの判断(ISO48-4)
3.4 HSM処理
レファレンスとなる基準製法(AEM1、FKM1、NR1)は3.2で示した方法で加硫され、加硫されたゴムはHSM内で処理をされました。その後ふるいにかけ2つの粒径(500μmと250μm)に分類しました。
4 結果と考察
4.1 未加硫ゴムテスト
未加硫ゴムの粘度測定はテーブル6-8に記載しております。未加硫ゴムの粘度測定はテーブル6から8に記載しております。すべてのサンプルにおいてムーニー粘度とMDRテストによる最低トルクは完全にHSMサンプルの含有量に依存しており、HSMの量が多ければレファレンスと比べて粘度がより高くなっています。しかしながら図3で示しているように増加することが加硫中のゴムのパフォーマンスに大きな影響を及ぼしてはいないことがわかります。加えて加硫曲線はすべてのサンプルにおいて同じ流れを追っています。これは加硫時間二おいても変化がないという事になります。
すべてのサンプルはREP社製の小型射出成型機Microjectにて成形しました。成形時に金型へ射出する圧力に関して最大5%の違いがありました。
図3に示す加硫曲線において最大トルクはHSM含有サンプルは多少低くなっており、20%含有サンプルが一番低くなっています。のこりの10%含有の3サンプルはすべてがほぼ同じような値を示していますが、それでも200μmパウダーサンプルが一番高い値となっています。このことはより細かい粉がパフォーマンスにより良い影響を与える可能性を示唆しています。
4.2 加硫ゴムテスト
加硫ゴムテストの結果はテーブル9-11にまとめました。硬度に関してはHSM含有サンプルはすべて低くなっていますが、その差は3で収まっています。強度テストに関してはゴムの製法によって異なる結果が出ました。AEMは20%含有サンプルのみ破断強度は著しく低下していますが変形強度に関しては再生ゴム含有サンプルはすべて高くなるという結果になりました。
FKMの結果も破断強度は様々ですが、こちらも変形強度はレファレンスと比べてすべて高くなっています。AEM、FKMどちらも二次加硫を行ったサンプルの方が強度が低くなるという傾向が出ています。NRのケースではすべてのサンプルにおいてほぼ近い結果になり、パターンを見つけるのが難しい状態です。AEMとNRの引裂き抵抗に関してはレファレンスと比べて重要な変化はみらませんが、FKMはFKM3のサンプルを除き低下していることがわかります。
5 結論
HSM脱硫プロセスを手短に紹介させていただきました。ここでは3種類(AEM、FKM、NR)のゴムを用いて実験的な検証を実施いたしました。各ゴムの物理的特性を調べたのちにHSMにて処理を実施し、処理されたゴムは配合パーセント,
粒度分布、また2次加硫品も加えるなど、条件を変えながらオリジナルのゴムと混ぜ合わせました。
各サンプルとオリジナルゴムとの比較結果では違いを見ることが出来ました。未加硫状態ではすべてのサンプルで粘度が上昇しましたが、この粘度上昇は射出までの工程において問題になることはありませんでした。サンプルにおける脱硫ゴムの割合はFKMとAEMの破断強度に関しては影響を及ぼしているが、NRに関してはそうではありませんでした。
同じ割合で脱硫ゴムを混ぜたサンプルにおいて脱硫ゴムの粒度違いでも比較をしました。粒度が細かいゴムを混ぜたサンプルの方がオリジナルに近い物性を示しました。そして2次加硫済みサンプルを混ぜたサンプルは最終的な物性においてネガティブな結果になっていました。このことはもう少し理由を検証していく必要があります。
すべてにおいて測定された変動値はそこまで大きくはなく、HSMゴムを混ぜて生産される製品はその性能を満足させられると思われます。もし物性として要求に満たない場合は小さな製法変更が必要になるかもしれません。オイルや可塑剤、加硫剤等を調整することで解消される可能性があります。
6 最後に
今回のプロジェクトにおいてサポートをしてくれたLRCCP(Laboratoire de recherches et de contrôle du caoutchouc et des
plastiques)のメンバーに感謝申し上げます。
そしてまたゴム材料を供給していただいたSACRED社とMr. P Dujon氏にも感謝申し上げます。
このプロジェクトの初期研究はNantes MétropoleとBPiFranceによってサポートされているECOTHERプロジェクトのフレームワークとして実施されました。
そして同時にこの研究はCIFRE(Industrial Convention of Learning by Research)協議、No.2014_01017によってANRT(French National Association for Research and Technology)が一部助成しております。
QRコードをスキャンしていただくことでこの記事の出典及び参考資料、文献をダウンロード可能です。
オリジナルの記事をご希望の場合はご連絡いただければ英語版を送らせていただきます。
その他REPに関する記事はこちら