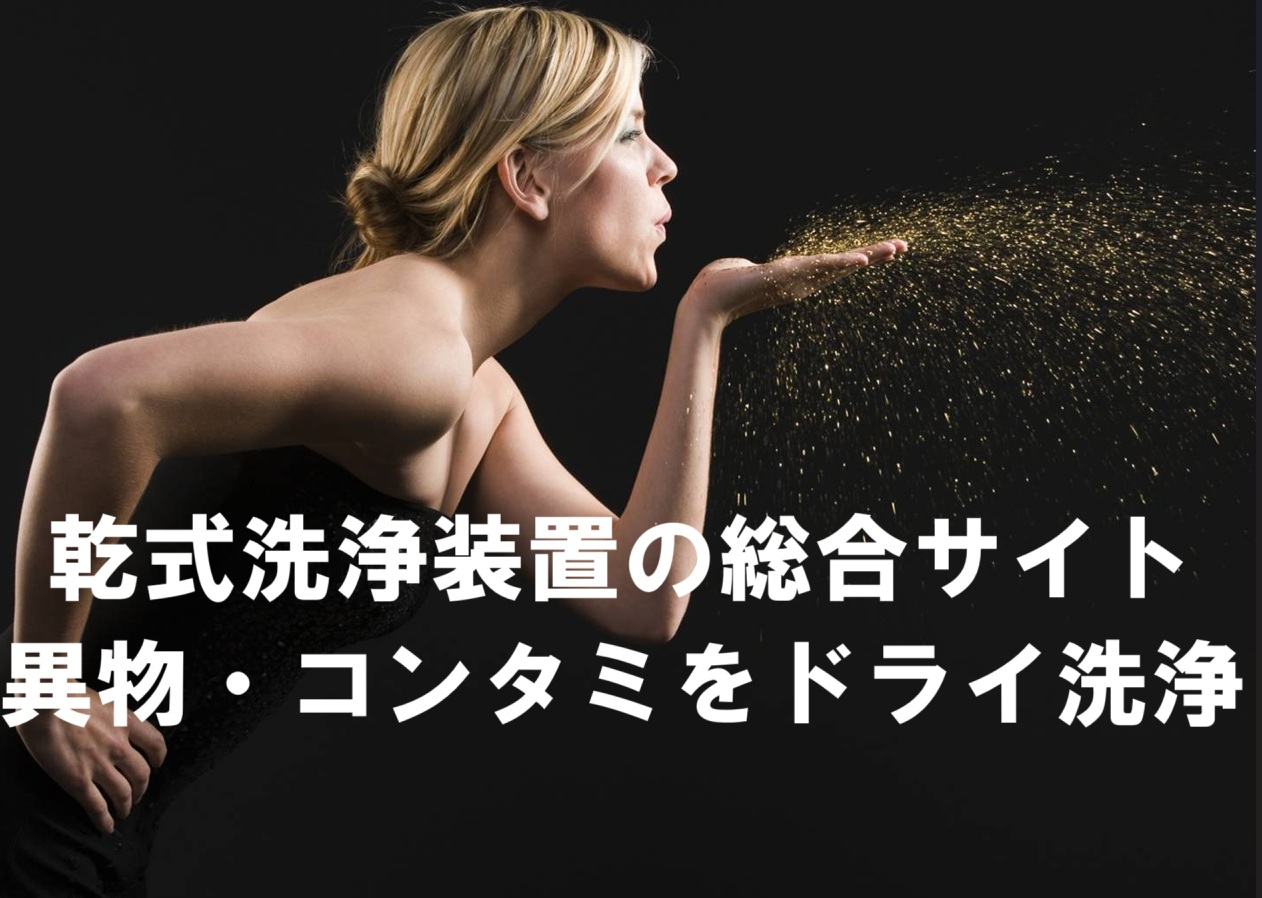
乾式洗浄は、湿式洗浄と異なり水・薬液を使わない洗浄方式の総称です。このサイトでは、除電器・除塵装置・非接触クリーナー・ウェブクリーナー・CO2スノードライ洗浄・大気圧プラズマ洗浄の用途・事例・選定のポイントをまとめました。製造現場の小さなゴミ・ホコリ・金属異物・コンタミ・脱脂の最新情報です。
目次
|| クリーンルームにゴミ・異物が持ち込まれてしまう
|| クリーンルームの中でも乾式洗浄のニーズがある
|| エアーブローノズル・吸引ノズルを設置しても異物を除去できないケース
|| 外注先からの納品物に異物が付着→生産現場に持ち込まれてしまう
|| 製造工程を変更したら異物の問題が発生した
|| 発塵源の特定化と対策だけでは問題に対処できないケース
|| 製造プロセス上の理由でどうしても発塵するケース
|| そもそも何が異物なのか分からないケース
なぜ乾式洗浄装置が必要なのか?
【タイプ別】乾式洗浄装置の種類・選び方
|| 手持ち式 クリーナー
ー除塵ピストル エレファント
|| ウェブクリーナー
ー非接触ウェブクリーナー(バックアップロール無)
ー非接触ウェブクリーナー(バックアップロール有)
ー回転ブラシ式ウェブクリーナー
||2D基材をクリーニング
ー非接触ウェブクリーナー スタティックエア
ー回転ブラシ式ウェブクリーナー ロータークリーン
ータイフンクリーン
||3D基材をクリーナー
ータイフンクリーン
||持ち運びやすいクリーナー
ーエレファントトローリー
||除塵ボックス
ー除塵ボックス(小容量)
ー除塵ボックス(中容量)
ー除塵ボックス(大容量)
||CO2スノージェット洗浄装置
||大気圧プラズマ処理機で乾式洗浄
【工程別】乾式洗浄装置の種類・選び方
積層工程 | 積載工程 | 切断工程 |
射出成型 | IMD・インモールド成型 | |
印刷工程(スクリーン印刷・パッド印刷・インクジェット) | ||
組立工程・アッセンブリ工程 | ||
コーティング工程・塗装工程 | ||
クリーンルームへ搬入前に乾式洗浄 | ||
巻取り工程 | スリット工程 | 脱脂 |
プレス加工 | 切削加工 | 研磨 |
レーザー溶接 | レーザー加工 |
【目的別】乾式洗浄装置の種類・選び方
【非接触搬送】は立派な異物対策です
|| 非接触浮上・非接触吸着の特徴
|| 非接触浮上・非接触吸着の用途
|| 製造現場の静電気 | 基礎から学び不良低減につなげよう!
|| 除電器・イオナイザの種類と選び方|4つのポイントで早わかり!
エアーフリー除電技術がカーボンニュートラルに貢献できる理由
エアーフリー除電技術は工場のSDGsへの取り組みの切り札!
製造現場ではゴミやホコリは様々な問題を引き起こす
製造現場では 微細なゴミ・ホコリ・異物・コンタミが製品に付着すると、加工時に不良を引き起こしたり、製品の品質低下・納品先でクレームの原因になったりと、様々な問題につながります。
そして、洗浄が不十分だと、製造プロセスで歩留まりが上がらず、ダウンタイム増加して、生産性が低下する可能性があります。
一方で、納品先からの品質への要求が少しづつ厳しくなっていくという傾向は、プラスチック・食品・電子部品・自動車部品・半導体など幅広い業界で聞かれます。お客様からの要求に適合する品質で製品を製造するために、発塵源を調査したりクリーン化を検討したり、製造現場へのゴミ・異物 持ち込みの防止策を講じるなど様々な取り組みが行われています。
◆例1:
半導体 後工程では、ウェーハをダイシングし 小片化したICチップを取り扱うプロセスでは、パーティクルの付着を最小限にする必要があります。真空パッド・吸着ノズル等でピックアップするにしても、接触部から微細なパーティクルが転写するかもしれません。どのようにピックアップして移載するか、コレット・吸着方法はどうするか、 最新の注意を払って選定します。
(参考:ICチップ・ダイを汚染・コンタミから守る非接触吸着技術)
◆例2:
電気自動車(EV)用 樹脂成型品を生産する工場では、組立後の最終形態が、樹脂製品が電子部品・プリント基板に近接することになるために 微細なコンタミ・特に金属異物が付着しないよう細心の注意を払って生産します。
(参考:電気自動車(EV)用 樹脂成型品の異物を除去する装置 )
◆例3:
ガラス基板・枚葉フィルム・シートの生産現場では、小さな異物付着は問題を引き起こす原因になるため、異物・粉塵を未然に防ぐため製造プロセスで適切な対策を施す必要があります。
(参考:ガラス基板・枚葉フィルム・シートを非接触で浮上・吸着する技術)
ゴミや異物の問題を解決できていない実情
|| クリーンルームにゴミ・異物が持ち込まれてしまう。
クリーンルームは、室内に浮遊している塵埃の濃度を、一定量に制御された空間です。クリーンルームは、室外よりも圧力を高くして(陽圧)、外部からの微粒子・パーティクルの侵入を防いでいます。そして、クリーンルーム内の空気は、フィルターを介して循環精製することで、室内の汚染物質を低減して、設計された清浄度になるようコントロールしています。
それでも、クリーンルームに汚染物質が持ち込まれてしまう事があります。それは、主にクリーンルームに行き来する人・モノを介して汚染物質が持ち込まれてしまうケースです。
クリーンルームに入室する時は、クリーンルームの清浄度により、段階的に衣類を清掃してから入室します。例えば、クラス10,000(ISOクラス7)のクリーンルームでしたら、入室前にすることは、おおよそ次のようになります。
・クリーンウェア(上下)・クリーンシューズ・キャップ・マスクを着用する
・クリーンルーム用 手袋を着用する
・粘着マットで靴底のゴミを除去する
・粘着ローラーでクリーンウェアをクリーニングする
・手を洗い、乾かし、手袋を着用する
・クリーンルーム用エアシャワーで身体をクリーニング
・室内へ入室
それでも、人からの汚染物質の持込を防ぐのは難しく、クリーンウェアの中の衣類からの繊維クズ、皮脂カス、毛髪、体毛、などが持ち込まれる可能性が残ります。
また、クリーンルームに持ち込む設備・器具等に 汚染物質がくっついて 室内に持ち込まれてしまうことも考えられます。
参考:クリーンルームへ搬入する部材の異物対策
|| クリーンルームの中でも乾式洗浄のニーズがある
クリーン環境の推進は、生産プロセスの清浄度を保持するために重要な施策ですが、製造現場のクリーン度が高い環境でも、ゴミやホコリの室外からの持込を完全に防ぐのは難しいのが実情です。実際に、除塵装置・ウェブクリーナーを、クリーンルーム・クリーンブース内に設置して使用している事例があります。クリーン環境の中でも、除塵装置を設置して局所的に付着異物を除去する施策の必然性があるようです。
◆例1
デジタルカメラや複合機のような、光学レンズ・電子部品を組み込む機器は、クリーンルームで組み立てられます。クリーンルームで、組立にしようする個々の部品を 除塵装置で表面の小さなゴミ・ホコリを除去するニーズがあります。
参考:プラスチック部品の異物対策|除塵ピストルで解決
◆例2
クリーンルーム内のロールtoロール工程で、塗工したPETフィルムを流しながらスクリーン印刷機を通すプロセス。フィルム表面の小さなパーティクル・塵埃が不良につながる可能性があるため、非接触ウェブクリーナーで小さな異物を除去するニーズがあります。
◆例3
最先端半導体製造用途のガラスは、クリーンルームで作られています。パーティクル・微粒子の付着を防ぐため、3Dクリーナー タイフンクリーンを使用するニーズがあります。
参考:クリーンルームで異物除去|電気自動車(EV) 樹脂成型品
|| エアーブローノズル・吸引ノズルを設置しても異物を除去できないケース
製造現場で、ゴミ・異物の問題に対処するため、エアーブローノズル・集塵フードを設置したり、除電器を設置したり、除塵装置を自作して対処したが、異物を除去できず 問題を解決できない ということがあります。
うまく異物を除去できれば良いのですが、デメリットもあります。
例えば、エアーノズル・集塵ノズルの設置位置、エアー圧・吸引風量・ダクトホース・ブロアの最適な条件出しには、作業者様の多大な労力と時間を要します。敷設するダクトホースから圧力損失を計算して最適風量を計算したり、用途に適したイオナイザの選定、エアーブローと吸引のバランス、、、リサーチするのも大変な作業です。
除塵装置を自作する場合は、設計に要する時間・労力を伴いますが、それに見合った成果を上げたいものです。
または、初めから装置化された除塵装置・乾式洗浄装置の導入を検討して、効率的に導入計画を進める方法があります。
参考:非接触クリーナー|異物除去・静電気対策のための除塵装置
参考:エアーブロー・吸引ノズルで除去できない粉塵をドライ洗浄する技術
|| 外注先からの納品物に異物が付着→生産現場に持ち込まれてしまう。
外注先へ部材を発注して、納品されたとき、発注した部材に異物が付着しているケースがあります。この部材をそのまま生産現場へ搬入すると、付着した異物が生産現場へ一緒に持ち込まれることになります。
対処するためには、外注先で異物対策するか、納品された後 自社で洗浄して対処する、どちらかです。納品・受け入れ後に、自社で洗浄する場合、装置化された除塵装置・クリーナーを導入して 対応する方法があります。
まず、納品・受け入れ後に、
◆生産現場に持ち込む前に 除塵装置・クリーナーで部材表面をクリーニングする、
↓
◆生産環境に持ち込んだ後、目的の工程で除塵装置・クリーナーで乾式洗浄する、
このような段階的に対処する方法があります。
参考:クリーンルームへ搬入する部材の異物対策
参考:除塵ピストル|パルスエアーブロー+静電気除去+異物吸引
|| 製造工程を変更したら異物の問題が発生した
技術は日進月歩。モノづくり・製造方法は、絶えず変化していきます。
モノづくり・製造方法に変更・改良が加わると、異物の問題が発生する可能性があります。
例えば、電気自動車向けに樹脂成型品・部品を生産する計画を立てる場合、異物対策がテーマになる可能性があります。電気自動車は、ガソリンエンジン車と比較して、電子部品・プリント基板・ケーブル・配線・コネクタが多く使用されています。これらは、小さな金属異物・コンタミから保護する必要があるため、樹脂成型品にも異物対策する必要が出てくるためです。
電池材料の生産では、技術的な進歩が速いので、原材料が変更されたり、新しい製造方法に変わることがあります。製造方法に改良が加わると、異物の問題が新たに発生する可能性があります。
このような工程変更・ライン改造のタイミングで、新たな異物問題が発生して、異物対策に取り組む というケースがあります。
参考:3Dクリーナー タイフンクリーン
|| 発塵源の特定化と対策だけでは解決できないケース
異物が製造プロセスから発塵したものであった場合、発塵源を特定化して問題を解決する必要があります。問題が発生した工程と、それ以前のプロセスを中心に、ラインや機械を全て見直し、原因の可能性を洗い出していく作業です。生産計画により、ラインを止められない期間は、点検作業はできません。生産の合間に、作業者が製造機械や製造プロセスの設備を一つ一つ入念に確認していきます。
原因を発見したあとは、対策を講じる前と後の比較を行い、効果を検証する作業を行います。しかし、どのように検証するかが難しい事があります。例えば、対策を講じたあと、製品が加工させるまで検証ができないような場合です。その場合、対策後に検証するためのサンプルを採取するまで長い時間を要し、そして、十分なサンプルを採取して検証する必要があり作業をより複雑化していきます。このように原因の究明は、多くの時間と労力を要する作業なのです。
発塵源を特定化して、改善策を講じることができれば、問題が起きていた工程に除塵装置を導入する必要はなくなるかもしれません。しかし、発塵源の特定化と対策が難しいケースもあり、問題が起きている工程に 3Dクリーナーを導入して局所的に除塵対策を講じる必然性があるのです。
|| 製造プロセス上の理由でどうしても発塵するケース
ウェブを所定の幅に裁断するプロセスとして、スリット加工というプロセスがあります。フィルム・紙・金属箔・炭素繊維複合材の製造プロセスにはスリット工程があり、多くの場合、スリッターでは、金属製の刃で基材を裁断するので切粉・スリットカスが発生します。スリット加工では、刃で裁断する箇所からの切粉の発生を防ぐのは難しく、パーティクルが発生した後にウェブクリーナー・静電気除去装置が必要になります。
(エッジのスリッター切粉を除電ブロー+吸引除去するクリーナー をみる)
(スリットカスを除去する3つの方法|切粉の問題はこれで解決!をみる)
(ロールスリッターでフィルムの静電気対策をみる)
また、ガラス基板の製造プロセスでは、プロセス上の理由でどうしても表面に粉塵が発生することがあります。ガラスの成分に由来する細かいガラス屑が表面に付着ような場合です。このような場合には基板を加工前にウェブクリーナー・3Dクリーナーで除塵する必要性があります。
(パネル・ガラス基板の異物対策・静電気対策をみる)
(ガラス基板をドライ洗浄する革新的な技術 をみる)
|| そもそも異物が何なのか分からないケース
基材の表面にコーティングする工程では、塗工面に小さなホコリや設備から発塵した金属カスなどが表面に付着すると、コーティングした後の表面に小さな突起物が現れて外観不良を引き起こすことがあります。コーティングした後でないと不良に気づけない場合、問題は難しくなります。不良に気づいたときには塗工した後なので、付着物が何なのか分からないのです。もし、異物が何なのか特定できれば、異物の材質(樹脂カス、SUS系金属カス、有機物など)から発生源を調べていく方法がありますが、コーティングする前に付着したどの異物が不良を引き起こしたものなのか、特定ができないと 発塵源を追跡することが難しくなるのです。
突起物が現れた箇所を切り取って、成分分析にかける方法があります。分析機関での調査に要する時間・コストが発生します。分析して異物の成分を特定できれば、発塵源の特定化の方向性が見えてきますが、分析や調査に要する負担が大きいので、局所的に除塵装置を導入して対応することができれば、除塵装置が 問題に一番迅速に対処できる方法になる可能性があります。
なぜ乾式洗浄装置が必要なのか?
乾式洗浄装置を導入するメリットは、
異物対策が必要なプロセスに設置して、局所的に洗浄できることです。
例えば、組立工程で個々の樹脂成型部品を組み上げる前に、表面の小さな粉塵・ゴミを除去したい、二次電池製造工程で正極材・負極材の金属異物を積層前に除去したい、という時に、装置化された除塵装置を設置して対処する施策があります。
生産環境そのものをクリーン化して、異物・コンタミの問題を防ぐ施策もございます。しかし、クリーンルームに出入りする人員は、毛髪・皮膚カスの発塵源になり、クリーンウェアを装着していても、わずかな毛屑・糸くずの発塵の可能性が生じます。すると、クリーンルームの中でも、除塵対策の必要性がでてきます。このようなケースでは、クリーンルームに持ち込む前に部材をクリーニングしたり、クリーンルームの中で部材をクリーニングする、という方法があります。
発塵源を特定化して、改善策を講じることができれば、問題が起きていた工程に除塵装置を導入する必要はなくなるかもしれません。しかし、発塵源の特定化と対策が難しいケースもあり、問題が起きている工程に 除塵装置を導入して局所的に除塵対策を講じる必然性があるのです。
このような背景から、ゴミ・異物・コンタミ対策が必要な工程に、乾式洗浄装置を設置すれば、ピンポイントでコンタミ対策を講じることができます。
乾式洗浄装置は、用途に応じて いろいろな装置があります。例えば、スリッターで切粉の吸引除去に適したモデル、樹脂製品に付着したホコリを立ち作業で清掃するのに適したモデル、製品を入れ物(トレー)に乗せる時 トレーの清掃に適したモデル、無風で静電気の局所除電に適したモデル、、、
自分が探している乾式洗浄装置をどうやって選定したら良いか、次の章で【種類・選び方】を説明します。
【タイプ別】乾式洗浄装置の種類・選び方
|| 手持ち式 クリーナー / 除塵ピストル エレファント
除塵ピストル エレファントは、手持ち式のグリップを操作して基材のクリーニングができます。「静電気除去+パルスエアーブロー+異物吸引除去」機能があります。
|| ウェブクリーナー
ー非接触ウェブクリーナー(バックアップロール無)
非接触ウェブクリーナー スタティックエアは、バックアップロールが無い 中空 の箇所に設置できます。フィルム・箔・電極 の異物対策の用途があります。
ー非接触ウェブクリーナー(バックアップロール有)
非接触ウェブクリーナー クロスジェットは、バックアップロールに抱かせて使用します。ミクロンオーダーのパーティクルの除去の用途があります。
ー回転ブラシ式ウェブクリーナー
回転ブラシ式ウェブクリーナー ロータークリーンは、「回転ブラシ+静電気除去+エアーブロー+異物吸引除去」機能があります。やや固着した異物・コンタミの除去に威力を発揮します。
||2D基材をクリーニング
ー非接触ウェブクリーナー スタティックエアには、枚葉シート・ガラス基板・プリント配線板をクリーニングする用途があります。
写真:非接触ウェブクリーナー スタティックエア
ー回転ブラシ式ウェブクリーナー ロータークリーンには、枚葉シート・ガラス基板・プリント配線板をクリーニングする用途があります。
写真:回転ブラシ式ウェブクリーナー ロータークリーン
ータイフンクリーンには、枚葉樹脂シート・複合材シート・ガラス基板をクリーニングする用途があります。
動画:タイフンクリーンで枚葉紙をクリーニング
||3D基材をクリーナー
ータイフンクリーンには、実装プリント基板・樹脂成型品・トレー・バイポーラプレートをクリーニングする用途があります。
||持ち運びやすいクリーナー
エレファントトローリーは、ホイールが付いており移動が簡単です。いろいろな現場へ持ち運んで使用するのに便利です。異物を除去する原理は、除塵ピストルエレファントと同じです。
||除塵ボックス
ー除塵ボックス(小容量)
除塵ボックス ウニマスター160は、小さなプリント基板・レンズ・ガラス・樹脂成型品をクリーニングするのに適しています。
写真:除塵ボックス ウニマスター160
ー除塵ボックス(中容量)
除塵ボックス ウニマスター210は、小さなプリント基板・レンズ・ガラス・樹脂成型品をクリーニングするのに適しています。
動画:除塵ボックス ウニマスター210
ー除塵ボックス(大容量)
イオン洗浄スペース ウニマスターは、大きな作業空間の除塵ボックスです。大型の樹脂成型品・トレーをクリーニングするのに適しています。
写真:イオン洗浄スペース ウニマスター
||CO2スノードライ洗浄装置は、二酸化炭素の結晶(CO2スノー)を噴霧して、油膜・接着剤の残渣・指紋・有機物・フラックス・ハンダボール・パーティクル・微粒子 等のコンタミをドライ洗浄する装置です。
写真:CO2スノードライ洗浄装置で、プリント基板をドライ洗浄
||大気圧プラズマ処理機で乾式洗浄
大気圧プラズマ処理機には、二つの用途があります。
①接着性・濡れ性を向上
大気圧プラズマ処理機で樹脂・プラスチックの表面を処理すると、官能基が形成されて、「接着性・濡れ性」を向上させることができます。
②プラズマ洗浄
大気圧プラズマ処理機には、薄い油膜・有機物を洗浄する効果があります。水・薬品・IPAを使わない乾式洗浄です。
動画:銅箔の酸化物を大気圧プラズマ処理機でドライ洗浄
【工程別】乾式洗浄装置の種類・選び方
|| 積層工程
シート状の箔を重ね合わせていく積層工程では、シートにパーティクルが付着したまま積層すると、異物を含有して積層してしまいます。例えば、二次電池製造プロセスでの電極材の積層プロセスでは重大な不良の原因になります。タッチパネルなどに適用されるシートの積層プロセスの場合、パーティクルの含有が外観不良や製品不良の原因につながります。
|| 積載工程
搬送キャリアに部品をロボットで積載するプロセスがあります。搬送キャリアに異物が付着していると、積載後に異物が製品に転写する原因になり、後工程で様々な問題を引き起こす原因になります。例えば、製品が電子部品の場合、トレーに付着していた異物が積載時に回路へ転写すると製品不良の原因になります。光学部品の場合、搬送キャリアから異物が転写すると、後工程で不良の原因になることがあります。
(治具の清掃を自動化する除塵装置をご紹介!をみる)
(除塵ピストル|樹脂トレイの異物除去|吸引+パルスエアーブロー+除電+ブラシをみる)
|| 切断工程
プリント基板製造工程には、回転丸刃で板を所定の寸法に切り出す切断工程があります。切断面は、刃と基板間の摩擦により強く静電気を帯びます。切断により、切粉が発塵して基板の表裏に付着していきます。このように粉を付着したまま基板が次工程へ搬送されると、不良率上昇・歩留まり低減の原因になります。
(プリント基板のフラックスをドライ洗浄!CO2スノージェット洗浄装置をみる)
(プリント基板のコンタミをCO2スノーでドライ洗浄をみる)
(実装プリント基板の切粉・樹脂カス・ガラス屑を非接触ドライ洗浄をみる)
(プリント配線板(PWC)の付着異物対策をみる)
(プリント回路板(PCB)の付着異物対策をみる)
|| 射出成型
射出成型機でプラスチック部品を金型で成型する現場では、金型を開いて部品を取り出すプロセスに静電気によるトラブルの原因が潜んでいます。開いた金型から部品を吸着パッドで取り出すときに部品が突き出しピンや金型内に静電気で貼り付いて取れ出せない問題が生じることがあります。これは、成型不良の増加や、警報で成型機が停止した場合にはメンテナンスによるダウンタイム増加につながります。
(除塵ピストル|樹脂成型品の異物除去|パルスエアーブロー+除電+吸引+ブラシをみる)
(樹脂成型品のコンタミをドライ洗浄をみる)
(プラスチック製品の成形工程で静電気対策をみる)
|| IMD・インモールド成型
IMD・インモールド成型は、成型機の金型の中で、樹脂部品やプラスチック部品に装飾フィルムの絵柄を転写して部品を加飾します。成型後に金型を開くと、インクカス・フィルムカスが浮遊して金型に付着することがあります。こうして金型に付着した異物は、次の部品を成型するときに、外観不良の原因につながります。
(ホットスタンプ後の樹脂成型品のバリ取りをみる)
(ホットスタンプして加飾した製品の箔バリを除塵をみる)
(射出成型機の金型の中を除電をみる)
|| 印刷工程(スクリーン印刷・パッド印刷・インクジェット)
印刷対象物に絵柄を描画する工程を印刷工程といいます。印刷工程で絵柄や印字が基準に達していないものは印刷不良となります。印刷不良は、納品先でのクレームの原因になる他、生産ラインのダウンタイム増加による生産性低下、歩留まり低減の原因になるので、不良率削減のため対策が必要になってきます。
印刷不良には、グラビア印刷の場合、ドクタースジやフィルムの静電気によるインキ飛び、ホコリ・塵埃が付着したフィルム面に印刷することによる印刷不良があります。
スクリーン印刷では、印刷物が静電気で浮遊しているホコリや微粒子をひきつけて、その表面にスクリーンを押し付けることで印刷外観に影響を及ぼすことがあります。そして、スクリーンメッシュが印刷物と接触・剥離することで剥離帯電による静電気が発生します。静電気はインキをはじくことでピンホールの発生原因になり、はじいたインクがメッシュを詰まらせることで印刷不良の原因になります。
(オフセット印刷で紙の静電気対策をみる)
(スクリーン印刷で樹脂フィルム・紙の静電気対策をみる)
(商業用デジタル印刷機で静電気対策をみる)
部品を組み立てていく工程で、部品に異物が付着していると、組立後の製品の中に異物が混入します。最終製品の形態により、このように付着した異物が重大な製品不良の原因になることがあります。例えば、最終製品が、レンズや光学部品を搭載した電子機器の場合、組立時に混入した異物が浮遊してレンズへ付着する可能性があります。レンズへの異物付着は最終製品の性能劣化につながり製品不良の原因になります。
(プラスチック部品の付着異物対策!の事例をみる)
(レンズのコンタミをCO2スノーでドライ洗浄 をみる)
組立工程では、大量のOリングを用意して、製品に組み込んでいくプロセスがあります。
小さなOリングは、振動コンベヤで搬送されるときに、互いに擦れあい、静電気を帯びています。静電気は、生産環境中に浮遊しているゴミやホコリを引き寄せて表面に付着させていきます。Oリングに、ホコリ・ゴミ・切削屑・金属粉などが付着していると、製品に取り付けて組み込んだあとにトラブルにつながる恐れがあります。
例えば、Oリングに小さなホコリが付着したまま、配管接続部に取り付けてシールすると、小さな隙間がリーク源になり、シール不良につながる原因になります。このようなトラブルを防ぐために、組立工程・アッセンブリ工程で使用する個々のOリングはきれいに清掃して、付着異物を除去する必要があります。
(大量のOリングをまとめてきれいにするクリーナーをみる)
|| コーティング工程・塗装工程
実際の生産環境では、例えばシートやパネルの表面に落下塵が付着したり、パネルの表面が静電気を帯びていたため空気中の浮遊塵を引き寄せて表面に付着することがあります。このようにして表面に粒子が付着したシート・パネルにコーティングすると、塗工後の表面に小さな突起物ができ、外観不良の原因につながります。
(パネル・ガラス基板の異物対策・静電気対策をみる)
|| クリーンルームへ搬入前に乾式洗浄
クリーンルームに部材を持ち込む時は、部材と一緒にゴミ・異物を一緒に持ち込まないよう注意が必要です。クリーンルームへ搬入する前に綺麗にクリーニングする必要があります。EV(電気自動車)向け部品の組み立てをクリーンルーム・クリーンブースで行うときには、クリーンルームへ搬入する前、クリーンルームの中で部材をクリーニングする用途があります。
これにより、クリーンルームの清浄度を保持し、組立時に製品が異物を含有するのを防ぐことにつながります。
(クリーンルームで異物除去|電気自動車(EV)用 樹脂成型品)
(クリーンルームへ搬入する部材の異物対策)
(クリーンルーム専用集塵機|世界初の技術で室内を綺麗に!)
|| 巻取り工程
箔・フィルム・紙に所定の加工を施したあと、基材を巻取りボビンに巻き取っていく工程があります。加工後のフィルムに切粉やパーティクルが付着していると、それらの異物を含有して巻き込んでいくことになります。このボビンが出荷され、納品先の現場で巻き出していくと、異物が表面に付着したまま送り出され、後工程で問題を引き起こし、クレームの原因になります。
(巻取ロールの静電気を効率よく除電する方法をみる)
(巻出ロールの静電気を効率よく除電する方法をみる)
(フィルム巻取り工程で静電気対策をみる)
(フィルム巻き出し工程で静電気対策をみる)
|| スリット工程
製造・加工したフィルムや箔を、所定の幅に裁断するためにスリット工程で処理します。スリット工程は、スリッターという機械の金属刃でウェブを決まった幅に裁断したり、不要な耳を切り落としていくプロセスです。刃でスリットすると、スリットカス・切粉というパーティクルが発塵し、フィルムの端面や表裏に付着するので巻き取る前に除塵する必要があります。巻き取ったボビンが納品先の現場で巻き出していくと、異物が表面に付着したまま送り出され、後工程で問題を引き起こす原因になります。
(エッジのスリッター切粉を除電ブロー+吸引除去するクリーナーをみる)
(スリットカスを除去する3つの方法|切粉の問題はこれで解決!をみる)
(ロールスリッターでフィルムの静電気対策をみる)
|| 脱脂
CO2スノージェット洗浄装置には、金属部品やプラスチック部品の油の被膜をドライ洗浄する用途があります。
|| プレス加工
フィルムや箔をプレス機の金型で打ち抜いてシートにする工程では、端面からカスが発塵する場合があります。カスがシートの端面や表裏に付着したまま積み重ねて梱包・出荷すると、納品先でクレームの原因につながります。
(プレス加工品の金属異物をインライン自動クリーニング)
|| 切削加工
CNCフライス、マシニングセンター では、切削加工中に発生する切りくずは、工具への巻きつきや切削熱による溶着の原因になり、工具寿命の低下やダウンタイムの増加につながります。クーラントとして、エアブロー・水溶性切削油・高圧クーラント・炭酸ガスブラストなどがあります。被削物・工具など切削条件を踏まえて、用途に適したクーラントを適用して、切削加工中の切り屑を除去しながら、冷却・潤滑を行う必要があります。
(クーラントに炭酸ガスを適用!ドライ切削加工の新技術をみる)
|| 研磨
CO2スノージェット洗浄装置には、レンズを研磨したあとの レンズ表面の研磨剤の残渣をドライ洗浄する用途があります。
|| レーザー溶接
CO2スノージェット洗浄装置には、レーザー溶接する前に部材表面をドライ洗浄する用途・レーザー溶接後の部材表面をドライ洗浄する用途があります。
|| レーザー加工
レーザー加工の前後で基材表面を洗浄するのは重要です。レーザー加工前の表面に薄い油分・金属粉塵があると、レーザー加工後にピンホール・外観不良・接合不良の問題につながる恐れがあります。
また、レーザー加工は ヒューム・煙・微粒子・すす・パーティクル・粉塵が発生することがあります。レーザー加工時 または レーザー加工後に表面を洗浄する用途があります。
(3Dクリーナータイフンクリーンには、バイポーラプレートをレーザー加工後に乾式洗浄する用途があります)
(ウェブクリーナー スタティックエアには、薄膜太陽電池をレーザー加工時にクリーニングする用途があります。)
(CO2スノーでレーザー加工後のヒュームをドライ洗浄)
(スタティックエアには、薄膜太陽電池の部材にレーザー加工時の蒸散物を吸引除去する用途があります)
【非接触搬送】は、立派な異物対策です
製造している製品を取り扱うとき、製品とモノが接触します。
例えば、ローラーコンベヤでガラス基板を搬送すると、ガラスとローラーが接触しますし、ウェーハを搬送するのに吸着パッドを使用すると、ウェーハとパッドが接触します。そして、接触する事により 小さな異物が製品に「転写」するリスクがあります。これが、「接触式」搬送に伴う問題です。
それに対し、「非接触」で製品をハンドリングする方法があります。製品に触れずに搬送することができれば、モノとモノが「接触」することに伴う異物転写リスクを回避することにつながります。
非接触で製品をハンドリングする技術に、(独)ZS-Handling社が開発した 超音波 非接触 浮上・非接触 吸着 技術があります。
ガラス基板・ウェーハ・ICチップ・枚葉樹脂シートのような表面がフラットな基材の搬送に限定されますが、これら平滑な基板に対して「非接触」で吸着したり 移載する用途に適用することができます。
<非接触浮上・非接触吸着の特徴>
◆基板に触れずに取り扱うことができるので、「接触」に起因する異物・コンタミ・パーティクルが転写リスクを回避します。繊細な基板を清浄度を保持して取り扱うことができます。
◆「非接触」なので、「接触」に起因する擦り傷・スクラッチのリスクを回避します。枚葉光学フィルムを搬送する用途のように、繊細な表面に対して優しいハンドリング技術です。
◆割れやすいウェーハ・ICチップ・ガラスチップを安全に移載します。
<非接触浮上・非接触吸着の用途>
ICチップ・ダイ | ウェーハ | ガラス基板 |
ソーラーウェーハ | レンズ | 検査機のステージ |
電極(正極材・負極材) | 枚葉フィルム・シート | フラットパネル(FPD) |
非接触コンベヤ | ピックアンドプレース | フリップチップ |
動画:ガラス基板を超音波非接触浮上
※エアーブローしてません。超音波が圧力が高い空気膜を形成し、その上をガラス基板が浮上しています。スクイーズ膜効果の原理です。
超音波 非接触 浮上・非接触 吸着 技術を見る
製造現場の静電気 | 基礎から学び不良低減につなげよう!
除電器・イオナイザの種類と選び方|4つのポイントで早わかり!
エアーフリー除電技術がカーボンニュートラルに貢献できる理由
エアーフリー除電技術は工場のSDGsへの取り組みの切り札!