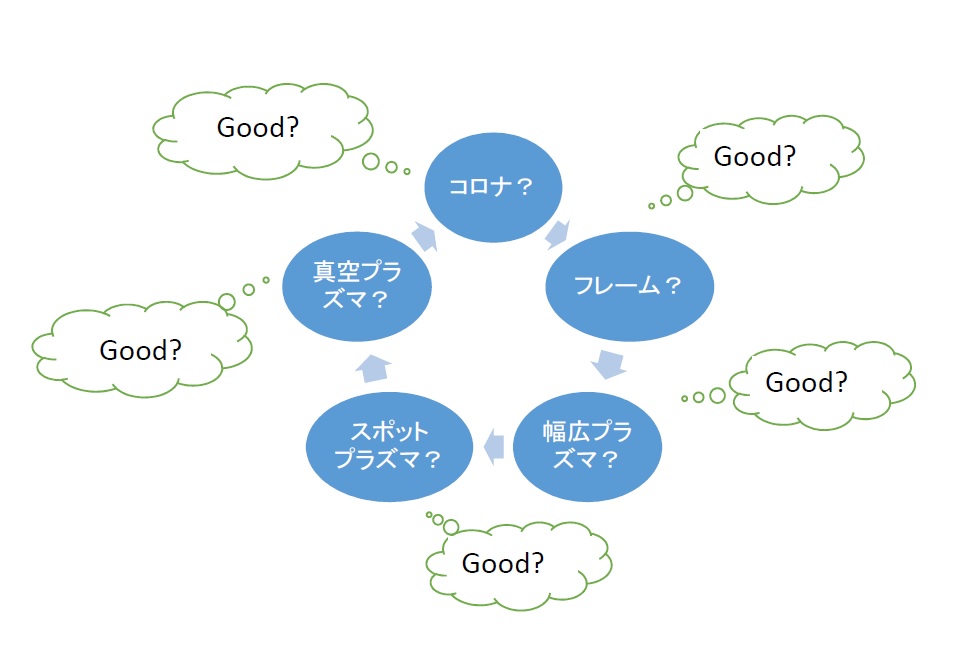
コロナ表面の特徴
スポット型大気圧プラズマ処理の特徴
幅広型大気圧プラズマ処理の特徴
真空プラズマ処理の特徴
フレーム処理の特徴
各処理機の主な用途
この用途にはどれ?
各種処理の比較
最後に
はじめに
弊社が取り扱っている表面処理機は、どの用途に適しているかという質問をよく受けます。
お客様の中には、プラズマでなければならないという固定観念を持たれている方もいらっしゃいますが
多くのアプリケーションが複数の処理機で対応できるため、ベストな選択肢を見極める必要があります。
ここでは大まかにどのような用途にどの機械が使えるのかを紹介します。
※特定の情報が知りたい方は目次から希望の箇所へ移動お願いします。
コロナ表面の特徴
コロナ処理はコンバーティング業界で広く使われている一般的な処理方法です。
イニシャル・ランニングコストが共に優れているため、表面処理を検討される際のベンチマークとなります。
既存のタイプであるフィルム向けのコロナ処理機の特徴は、下記のようになります。
簡単にコロナ処理の特徴を★印で視覚化しました。
詳しいメリットとデメリットはこちら↓↓↓
コロナ処理のメリット
トータルコストに優れている
・設備金額も他の処理機より相対的に安い
・電気のみでランニングコストも安価
幅方向への対応力が高い
・長尺物(数メートル幅のフィルム)も対応可
電気なので反応性が良い
・放電スイッチのオン/オフに反応してすぐに放電・停止することができる
改質度合いの制御がしやすい
・熱による形状変形・面劣化のリスクが少ない
・速度や出力の可変によって狭い範囲で一定の濡れ性を出しやすい
コロナ処理のデメリット
処理ムラがでやすい
・電気は流れやすいところに流れる性質があり、処理幅方向に均一性が劣る
薄いフィルムまたはシートのみ処理可能
・厚みが1mmを超えると放電が難しいため、処理対象がウェブ状製品に限られる
感電の危険がある
・高圧・高電流のため、感電対策が必要
オゾン対策が必要
・大量のオゾンが発生するため触媒や局所排気装置が必要
・環境オゾン濃度を0.1ppm未満に保つ必要がある
帯電の可能性がある
・機材表面に電気的エネルギーが付与され、静電気が帯電することがある
機材表面を傷つけてしまう
・機材表面に直接電気が流れるので表面を荒らしてしまう可能性がある
場合によってはスパーク痕が残る
ピンホールが発生してしまう
・電気は流れやすいところへ流れるため、局所的に多くの電気が流れることがある
・一部分だけ他より薄い・汚れがついている等、周りと違う場所に局所的に多くの
電気が流れることでフィルムを突き破る可能性がある
裏抜けが発生してしまう
・ロールtoロールでフィルムとロールの間に空間が隙間ができるとその空間で放電が発生し
裏面にも処理がかかることがある
処理能力が比較的低い
・1電極あたりの効果が相対的に低いので、電極の本数を増やす必要がある
スポット型大気圧プラズマ処理の特徴
プラズマ処理には大きく分類すると大気圧と低圧化で行う真空プラズマに分けられます。
大気圧プラズマも主に圧縮空気を利用するスポットタイプの大気圧プラズマ処理と
各種不活性ガス(窒素、アルゴン、ヘリウム等)を主として発生させる幅の広い大気圧プラズマがあります。
ここではスポット型のメリット、デメリットを紹介します。
スポット型大気圧プラズマ処理は電線やケーブル業界の印字の前処理、封止用途の接着前処理によく使われます。
近年ではスポット型でありながら、一度に処理できる幅を広げた改良版も見受けられます。
簡単にスポット型プラズマ処理の特徴を★印で視覚化しました。
詳しいメリットとデメリットはこちら↓↓↓
スポット型プラズマ処理のメリット
高速対応力がある
・処理幅に対しエネルギーが高いため(出力/処理幅)、改質効率が良い
・高速走行する基材でも改質させることが可能
処理対象物を選ばない
・プラズマ放電は無電位のため樹ほぼすべての材質に処理することができる
ランニングコストが比較的安い
・基本は圧縮空気を使用して処理を行うため高価な不活性ガスを用意する必要がない
自動化設備に組み込みできる
・放電ノズルをロボットやサーボに固定することで自動化設備の1つとして使用可能
スポット型プラズマ処理のデメリット
処理幅が限られる
・スポット型はノズルの処理幅が10mm前後のため、広幅処理に工夫が必要
・複数化や発展型の使用等
オゾン・NOx対策が必要
・プラズマ放電によりオゾンやNOxが発生するため、局所廃棄や触媒が必要
熱によるダメージを受ける可能性がある
・プラズマ放電による熱で基材がダメージを受ける可能性があり処理速度を遅くできない
幅広型大気圧プラズマ処理の特徴
スポットタイプと同じ大気圧プラズマ処理だが各種不活性ガス(窒素、アルゴン、ヘリウム等)を主として
用いて横方向に均一なプラズマを発生させる大気圧プラズマ処理です。
誘電体バリア放電を用いた無電位なプラズマを照射するタイプ、コロナ処理機の発展型として
電極間にガスを満たす有電位のプラズマ処理があります。
弊社が扱うタイプは無電位の幅広プラズマになります。
簡単に幅広型プラズマ処理の特徴を★印で視覚化しました。
詳しいメリットとデメリットはこちら↓↓↓
幅広型プラズマ処理のメリット
フィルムやシートを連続生産可
・スポット型とは異なり、コロナ処理機と同じような使い方で処理可。
ダメージレスで処理できる
・無電位タイプの場合、機材に電気が流れることがないので痛める心配がない。
・温度も低いため熱による変形の心配も非常に少ない。
均一性が高い
・電極内部でエネルギーを付与されたガスが放出されるため、幅方向に均一なプラズマ処理が可能
反応ガスを変えて違う効果を得ることができる
・通常は酸素ガスがメインだが、水素ガス等も使用可能
処理対象物を選ばない
・無電位タイプの場合、樹脂から金属まで材質を問わずに処理が可能
幅広プラズマ処理のデメリット
導入コストが割高
・工業用ガスを使用するため、設備金額に加えランニングコストがかかる
・他の処理方法と比べトータルコストが高い。
処理能力が比較的低い
・コロナ処理機同様、速度に対し処理効果が高くないため、高速処理には不向き
・処理回数を増やすなどの対応が必要
三次元形状には不向き
・フィルムやシートを想定しており、ロボットに持たせるには不向き
・多少の凹凸は工夫次第で処理可能
オゾン対策が必要
・オゾンが発生するため局所排気かオゾン触媒を用意する必要がある
真空プラズマ処理の特徴
真空プラズマ処理は半導体製造が増えていく過程で普及していった処理機です。
現在では他の処理方法がメインとなっていますが、用途や処理対象物によっては
大気圧方式よりも優れた特徴を有しています。
ここでは表面改質に用いられる2.45GHzのマイクロ波方式について紹介します。
簡単に真空プラズマ処理の特徴を★印で視覚化しました。
詳しいメリットとデメリットはこちら↓↓↓
真空プラズマ処理のメリット
処理対象物を選ばない
・無電位タイプの場合、樹脂から金属まで材質を問わずに処理可能
ランニングコストが安い
・様々なガスを使用して処理をするが使用量は少量のためランニングコストを抑制可
・外気(空気)を使用すればガス代をかけずに処理可能
小さい成形品の処理に最適
・小型(20-30mm程度)製品を一度に大量に処理できる
狭い隙間を処理できる
・大気圧で処理しにくい狭いエリアも真空では内側まで均一に処理可能
反応ガスを変えて違う効果を得ることができる
・通常は酸素ガスがメインだが、水素ガス等も使用可能
粉体の処理が可能
・大気圧下ではハンドリングが難しい粉体を減圧下で処理可能
真空プラズマ処理のデメリット
流れ作業には向かない
・バッチ処理中心のため既存の生産ラインにそのままでは設置が難しい
・自動投入取出を設計すればバッチでも全自動化は可能
設備単価が高い
・処理量で考えると設備の金額が割高
1工程の時間がかかる
・セット・真空引き・取り出しというプロセスがあり、処理に時間がかかる
・1度でどれだけの量を処理できるかが鍵
フレーム処理の特徴
フバーナーを変えることで様々な形状、幅に対応することができる高い柔軟性が特徴です。
また炎の長さを活かして凹凸のある成形品への処理に多く使われています。
簡単にフレーム処理の特徴を★印で視覚化しました。
詳しいメリットとデメリットはこちら↓↓↓
フレーム処理のメリット
高速処理に対応できる
・スポット型同様、高速でも改質可能
処理対象物を選ばない
・プラズマ処理同様に幅広い材料に対し利用可能
様々な形状の製品に利用できる
・バーナーの設計が自由なので、対象物に合わせ自由に組み合わせ可能
大型化にも対応できる
・幅広バーナー・大型発信機を供給可能
ガス種を選べる
・仕向地に合わせガスを選択可(プロパン、メタン、ブタン)
ロボットに持たせて自動化できる
・大型成型品の処理へも対応可能
フレーム処理のデメリット
低速で処理ができない
・高速での処理には強いが低速で処理を行うと熱によるダメージを与える可能性
熱ダメージの懸念がある
・低速での処理、極端に薄いフィルムや熱に弱い材料などは変形または劣化する可能性
火傷の危険がある
・燃焼している炎や消火直後のバーナーは高温のため、接触を避けるための対策が必要
火災の危険がある
・直火を出すため、処理エリア周辺に防火対策を施す必要がある。
各処理機の主な用途
コロナ処理機:コンバーティング用途、延伸フィルムなど薄いフィルム・箔
プラズマ処理機(幅広タイプ):フィルムや箔のロールtoロール、シート形状などの枚葉表面、小型成形品。
プラズマ処理機(スポットタイプ): 狭いエリアの表面処理、溝の中への処理、ケーブルや電線。
真空プラズマ処理機:小型の成形品や粉、少量多品種な製品。
フレーム処理機:凹凸がある三次元形状の製品や高速のフィルムや箔、また小型成形品のインライン処理
この用途にはどれ?
・安価な設備をお探しですか? →一般的なコロナ処理機をお選びください。
・ダメージレスで処理がしたいですか?→大気圧幅広プラズマ処理機をお選びください。
・速い速度でも高い濡れ性が欲しいですか?→フレーム処理機、または通常のコロナ処理機を複数台設置してください。
・薄いフィルムを処理したいですか?→大気圧幅広プラズマ処理機、一般的なコロナ処理機またはカウンターレスコロナ処理機をお選びください。
・裏抜けを避けたいですか?→カウンターレスコロナ処理機をお選びください。
成型品の表面処理を検討している場合
・凹凸はありますか?
→フレーム処理機または改良型の大気圧プラズマ処理機をお選びください。
・サイクルタイムは早いですか?
→フレーム処理機をお選びください。
・処理エリアは限られていて狭いですか?
→フレーム処理機かスポット型大気圧プラズマ処理機をお選びください。
・処理面は平坦ですか?
→フレーム処理機、カウンターレスコロナ処理機、噴出し型コロナ処理機からお選びください。
・小型のパーツですか?
→真空プラズマ処理機、フレーム処理機、改良型の大気圧プラズマ処理機などからお選び下さい。
・ブロー成型品ですか?
→フレーム処理機または改良型の大気圧プラズマ処理機をお選びください。
特殊な形状、材質の場合
・粉を処理したいですか?
→特殊真空プラズマ処理機をお選びください。
・紙業界向けのアプリケーションですか?
→紙の原反などをロールtoロールでの処理をお考えでしたらフレーム処理機をお選びください。
・電線やケーブルの印字前処理や転写防止用途ですか?
→スポット型の大気圧プラズマをお選びください。
・金属パイプや樹脂パイプなどの外周を処理したいですか?
→リングバーナーを用いたフレーム処理機、複数のノズルのスポット型の大気圧プラズマ処理機をお選びください。
上記の分類はあくまでも一例です。当てはまらないものは是非お気軽にお声がけください。
各種処理の比較
それぞれの処理方法の特徴が分かるようにすべての処理方法の★印をまとめた表です。
※このグラフは弊社が扱う設備が対象です。条件を変えることで変動いたします。
★1つがダメというわけではありません。
比較のために星の数に違いを付けております。
より詳しい情報は是非お気軽にお問合せください。
最後に
弊社押上分室にて、装置の実機をご覧頂きながらのお打合せも可能です。
ご来社をご希望される場合、下記フォームをご利用下さい。
ご来社相談フォーム
アポイントメントはお電話でも承っております。
表面処理とは?表面処理、プラズマ処理原理を説明したページです。
フレーム処理とは?フレーム処理に特化して原理を説明したページです。