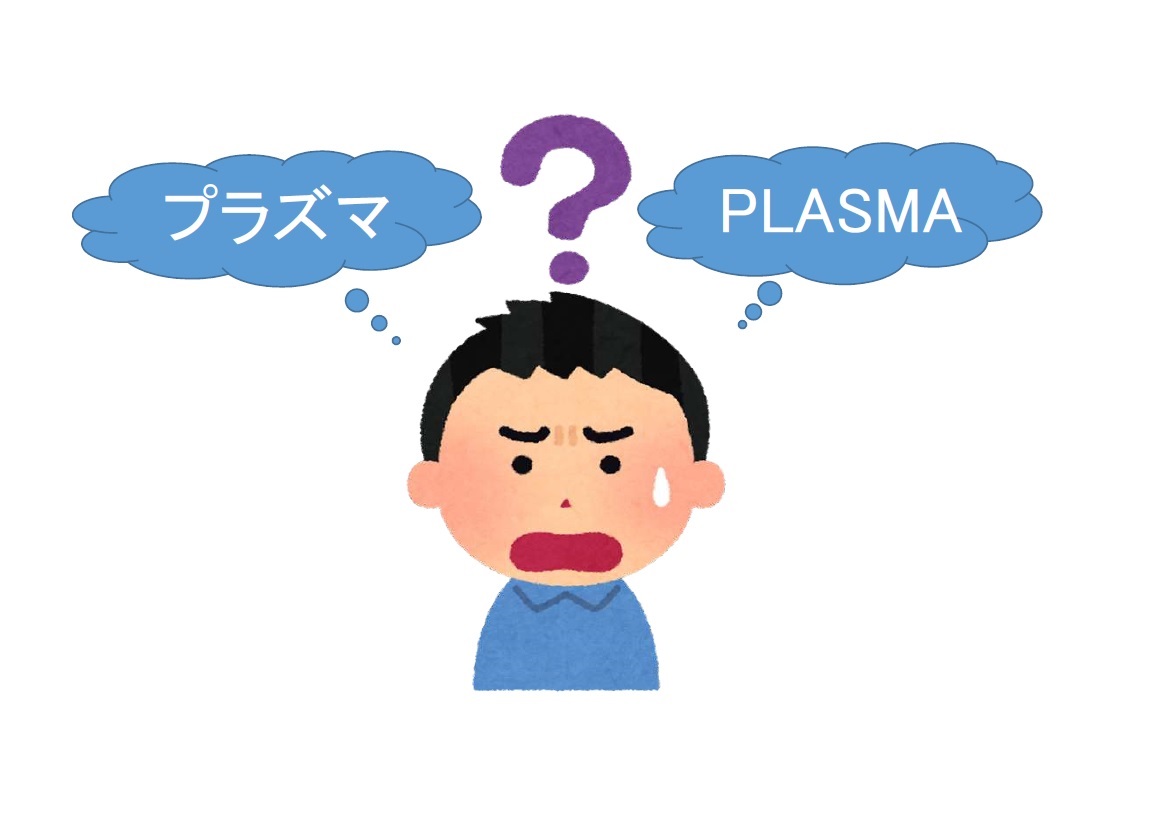
プラズマ処理とは、コロナ処理と同じように、電気の力で気体(主に酸素)をプラズマ化させ、ラジカルを樹脂などの表面に付与する処理方式です。
このページは、接着や密着、塗装の前処理としてのプラズマ処理の特徴をご紹介します。
関連ブログ
目次
はじめに
接着や密着、塗装の前処理としてプラズマ処理やフレーム処理、コロナ処理など様々な種類があります。
このブログでは、プラズマ表面処理に焦点をあてて説明します。
プラズマ処理
プラズマ処理は、コロナ処理と同じように、電気の力で気体(主に酸素)をプラズマ化させ
ラジカルを樹脂などの表面に付与する処理方法です。
プラズマ処理は、真空下で行う低圧プラズマ処理と、大気圧下で行う大気圧プラズマ処理の2種類の方法があります。
今では大気圧プラズマが一般的になりつつあり、一般的にプラズマ処理と言うと
大気圧プラズマを指す方が多いようです。
真空プラズマも大気圧プラズマも、使用するガスや放電方法の違いにより
設備の形状や用途が異なります。
コロナ処理との違い
そもそも「プラズマ」とは、物質の状態を表す言葉で、「コロナ」とは放電状態を表す言葉です。
コロナを含む様々な放電によって分子をプラズマ化するため、大きな視野でみると
「コロナ=プラズマ」とも考えられます。
実際は、「コロナ処理≒プラズマ処理」なのですが、明確な境界線はなく、少々曖昧です。
プラズマと呼ばれる処理機と、コロナと呼ばれる処理機の間の処理機も存在しています。
一般的な見分け方として「ガスを使用するか、しないか」という考えがあります。
弊社では、「ガス」を介して処理を行う設備はプラズマ処理機、ガスを介さずに処理を行うのがコロナ処理機と
考えておりますが、他メーカー様にはそれぞれの定義があると思うので、参考としてお考え下さい。
プラズマ処理の原理
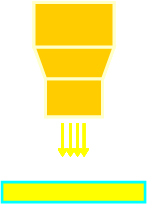
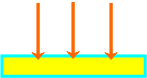
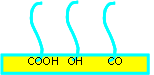
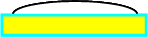
物質を電離させる、つまりイオンと電子に分離させることによって、プラズマを得ることができます。
電離させるために必要なエネルギーの供給方式により、3つに分けられます。
1:放電 (コロナ処理やプラズマ処理)
2:熱電離(フレーム処理)
3:光電離(UV処理)
空気中で放電することにより、空気中の酸素分子が解離し、酸素原子が励起して酸素イオンや
自由電子を含むプラズマが発生します。
発生したプラズマの電子・イオン・ラジカルが基材表面に接触します。
基材表面の分子とプラズマ中のイオン・電子が反応、親水性官能基が生成されます。
表面活性化が行われ、接着性やぬれ性が向上します。
(=分子間力、ファンデルワース力の働き)
なぜ濡れ性があがるのか
プラズマ処理を行うことで濡れ性(親水化)が向上しますが、下記の要因があります。
官能基の付与
ポリプロピレン・ポリエチレンなど特にオレフィン系の合成樹脂は、表面に極性基が無く
接着剤やインクなどに対して 親和性がありません。
放電により放出されたイオンや電子が樹脂表面の分子の化学結合を切断し、樹脂の種類に応じて
親水性の官能基 OH(水酸基)・CO(カルボニル基)・COOH(カルボキシル基)等が生成されます。
表面洗浄
アルコールや溶剤などのウェット洗浄でも落としきれなかった僅かな汚れ(特に有機物)と
放電により放出されたイオンや電子が結合することで分解洗浄されます。
もともとの表面が持っていたエネルギー値を引き出し、そしてその表面が官能基によって
活性化されることでも親水性が向上します。
主に金属への処理では表面洗浄によって濡れ性を引き出します。
プラズマ処理機の種類
プラズマ処理機(プラズマ処理装置とも呼ばれる)には様々な方式の物が存在しています。
大きく分けて真空か大気圧か、真空と大気圧でもそこから色々と分岐していきます。
プラズマ処理機とはプラズマを用いて行う様々な処理機の総称です。
スポット型大気圧プラズマ
大気圧プラズマと呼ばれると、このタイプのプラズマ処理を想像される方も多いと思います。
主に圧縮空気(窒素なども使用可能)を用いた処理方法で、先端の放電ノズル内で
高圧高周波の放電を行います。
その放電空間を圧縮空気などのガスが通過していく過程でイオンやラジカルへと変化し
最終的にそれらが混在した状態(プラズマ状態)のガスとなり、外部へ放出されます。
(ランテック社製大気圧プラズマ処理機PlasmaJet)
スポット型大気圧プラズマ処理機のメリット
・高速対応力がある
処理幅に対しエネルギーが高いため(出力/処理幅)、改質効率が良い
高速走行する基材でも改質させることが可能
(電線、ケーブル、金属パイプ等細くて高速で搬送されるもの)
・処理対象物を選ばない
プラズマ放電は無電位のため樹ほぼすべての材質に処理することができる。
(金属、樹脂、プラスチック、ゴム、エラストマー、セラミック、紙等)
・ランニングコストが比較的安い
基本は圧縮空気を使用して処理を行うため高価な不活性ガスを用意する必要がない
スポット型大気圧プラズマ処理機のデメリット
・処理幅が限られる
スポット型はノズルの処理幅が10mm前後のため、広幅処理に工夫が必要
複数化や発展型の使用等
・オゾン・NOx対策が必要
プラズマ放電によりオゾンやNOxが発生するため、局所廃棄や触媒が必要
・熱によるダメージを受ける可能性がある
プラズマ放電による熱で機材にダメージを受ける可能性があり処理速度をあまり遅くすることができない
派生型
基本的に10mm前後と狭いエリアしか処理ができない欠点を補うため
先端ノズルを回転させることで円の直径分の長さを処理ができるタイプがあります。
また、放電部分を連結させたようなノズル形状にし、複数ノズルを1つのノズルとして
処理幅を確保するタイプもあります。
弊社では回転タイプの派生版、または複数ノズルを1台の発信機で制御する
マルチタイプなどを取り扱っています。
(ランテック社製大気圧プラズマ処理機Plasphere)
派生型大気圧プラズマ処理機のメリット
・スポット型よりも広いエリアを1つのノズルでカバーできる
派生型大気圧プラズマ処理機のデメリット
・プラズマエネルギーが分散するため処理能力が低下するため高速対応力がスポット型よりも低くなる
・より広いエリアをカバーするため出力がスポット型よりも多くなる
幅広型大気圧プラズマ
幅広型大気圧プラズマは、光学フィルムや金属箔など表面ダメージを嫌う製品をロールtoロールで処理したい
またはコロナ処理よりも安定してフィルムを処理したいというニーズを満たす設備です。
主に使用するのは圧縮空気ではなく、窒素やヘリウム、アルゴンといった不活性ガスをメインに、
必要に応じて酸素や水素などの反応性ガスを添加して処理を行います。
放電のアノード・カソードを電極内に収納しガスのみを照射することで基材に電気的ダメージを与えない
無電位タイプと、コロナ処理のように処理対象物を挟み込む形状で、その空間内をガスで満たす
有電位タイプに分類されます。
この有電位タイプは、ガスで満たす以外はコロナと非常に類似しているため
ガスコロナ処理と呼ばれていた時期もありました。
(アクシス社製大気圧プラズマ処理機ULD)
無電位型
無電位タイプのプラズマ処理機は「リモート型」とも呼ばれることがあります。
高圧を誘電体バリアを通じ印加し放電空間を通過してプラズマ化したガスのみが外部へ照射されるため
ガスに電位がなく導電体へもダメージレスで処理ができるのが特徴です。
弊社が扱うフランスAcXys社の幅広プラズマは、特許取得の特殊構造を有した電極のため
一般的な無電位タイプのプラズマ処理と比べて効率の良い放電が可能となっています。
有電位型
有電位タイプは「ダイレクト型」とも呼ばれる方式です。
無電位のリモート型とは異なり、印加空間と処理エリアが同空間となるため
導電体への処理ができないというデメリットがあります。
コロナ処理のアップグレードとして、より効率的で均一な処理をロールtoロールで
処理ができるというメリットもあります。
弊社では有電位タイプの取り扱いがないため、無電位のプラズマのメリットとデメリットを紹介します。
幅広型大気圧プラズマのメリット
・フィルムやシートを連続生産可
スポット型とは異なり、コロナ処理機と同じような使い方で処理可。
・ダメージレスで処理できる
無電位タイプの場合、機材に電気が流れることがないので痛める心配がない。
温度も低いため熱による変形の心配も非常に少ない。
・均一性が高い
電極内部でエネルギーを付与されたガスが放出されるため、幅方向に均一なプラズマ処理が可能
・反応ガスを変えて違う効果を得ることができる
通常は酸素ガスがメインだが、水素ガス等も使用可能
・処理対象物を選ばない
無電位タイプの場合、樹脂、セラミック、そしてゴムや金属まで材質を問わずに処理が可能
幅広型大気圧プラズマのデメリット
・導入コストが割高
工業用ガスを使用するため、設備金額に加えランニングコストがかかる
他の処理方法と比べトータルコストが高い。
・処理能力が比較的低い
コロナ処理機同様、速度に対し処理効果が高くないため、高速処理には不向き
処理回数を増やすなどの対応が必要
・三次元形状には不向き
フィルムやシートを想定しており、ロボットに持たせるには不向き
多少の凹凸は工夫次第で処理可能
・オゾン対策が必要
オゾンが発生するため局所排気かオゾン触媒を用意する必要がある
真空プラズマ
真空プラズマは、処理チャンバー内を真空ポンプで減圧状態にした後に
様々なガスを投入することで処理を行うため、バッチ方式となります。
半導体業界の成長期にメインの処理機として大きく普及した設備です。
現在は大気圧プラズマが一般的になっていますが、真空プラズマにしかできない用途も多くあります。
真空プラズマも使用する周波数によって主な用途が分かれています。
※真空プラズマと呼んでいますが、完全な真空ではなく、極低圧で処理をするプラズマ処理を
一般的に真空プラズマと呼んでいます。一般的な処理圧力は10-50Pa程度です。
(ピンク社製真空プラズマ処理機V6G)
KHz型とMHz型
KHz型とは、40-100KHzの比較的低い周波数を使用するため、LFとも呼ばれています。
MHz型は、13.56MHzを使用し、RFとも呼ばれています。
LF・RF共に金属製の電極をチャンバー内に有しています。
この二つの周波数は金属電極へ向けてスパッタ効果を発生させる特徴があります。
そのためメタル電極から金属粒子が発生し、チャンバー内に拡散します。
MHzはこの特性を活かしてCVDなどに用いられています。
チャンバー内で自己バイアスが発生するため、電気的に繊細な部品などは
破壊してしまう恐れがあるため、処理をすることができません。
LF・RF共にアルゴンガスを用いる場合は、MWと比べてアルゴンイオンの動力学的エネルギーが
高いというメリットがあります。
GHz型
2.45GHzのマイクロ波(マグネトロンやMW)を用いる真空プラズマで
表面処理の用途として一般的に使用されています。
LFやRFよりもプラズマ密度が濃く、空間内が無電位であるため材質を問わず処理が可能です。
また、空間内が均一なプラズマ空間となるため、チャンバー内に入れることができれば
処理がかかるという点が他の周波数と違うメリットです。
しかしマグネトロンでは基本的にスパッタ効果は期待できません。
表面処理用途に用いる真空プラズマは、GHzのマイクロ波プラズマが主流であるため、
そのメリットとデメリットを紹介します。
真空プラズマのメリット
・処理対象物を選ばない
無電位タイプの場合、樹脂、セラミック、そしてゴムや金属まで材質を問わずに処理可能
・ランニングコストが安い
様々なガスを使用して処理をするが使用量は少量のためランニングコストを抑制可
外気(空気)を使用すればガス代をかけずに処理可能
・小さい成形品の処理に最適
小型(20-30mm程度)製品を一度に大量に処理できる
・狭い隙間を処理できる
大気圧で処理しにくい狭いエリアも真空では内側まで均一に処理可能
・反応ガスを変えて違う効果を得ることができる
通常は酸素ガスがメインだが、水素ガス等も使用可能
・粉体の処理が可能
大気圧下ではハンドリングが難しい粉体を減圧下で処理可能
真空プラズマのデメリット
・流れ作業には向かない
バッチ処理中心のため既存の生産ラインにそのままでは設置が難しい
一応自動投入取出を設計すればバッチでも全自動化は可能
・設備単価が高い
処理量で考えると設備の金額が割高。
大型化すれば製品単価/設備金額は安くなるが初期投資が大きくなる。
・1工程の時間がかかる
セット・真空引き・取り出しというプロセスがあり、処理に時間がかかる
1度でどれだけの量を処理できるかが鍵
プラズマ処理の用途
プラズマ処理といっても、各方式によって最適なアプリケーションが異なるため
主な用途となる分野をまとめてみました。
ロールtoロールでの処理
主にフィルムや金属箔といった薄い処理対象物表面の親水化、クリーニング用です。
プラスチックフィルムで有れば無電位、有電位両方のプラズマ処理が応用いただけますが
金属箔や表面ダメージを気にするフィルムには無電位タイプを推奨します。
シートや平らな製品を枚葉の処理
プラスチックシート、発泡製品、金属板等フラットな表面を処理する場合でも厚みがある場合
無電位タイプのプラズマをお使いください。
シートの幅によってはスポット型の発展版もご利用いただけます。
小面積の処理
処理幅が主に10mm程度の場合は、スポット型の大気圧プラズマをお選びください。
電線やケーブル、樹脂製品の封止用接着剤塗布の前処理など、処理エリアが限られる場合に適しています。
中面積の処理
処理幅はフィルムやシートほど広くはないが、スポット型では対応できない幅、50mm前後には
派生型をお選びください。派生型ノズルを複数組み合わせれば100mmを超える幅も処理可能です。
粉体の処理
樹脂や金属の粉を大気圧で処理することも可能ですが、量産を考慮すると真空化での処理が合理的です。
弊社では1度に10㎏前後(PEパウダー)処理が可能な設備を取り扱っております。
今まで金属パウダー、セラミックパウダーなど様々な粉体に挑戦してきました。
最後に
広く知られている「プラズマ処理」という言葉が用いられる設備でも、実は様々な方式があり
各設備に得意分野が存在しております。
プラズマ処理を検討したけど使えなかったという結論が出た場合でも、実は異なるプラズマなら
しっかりと対応できるケースがあります。
貴社のアプリケーションに応じて適切な設備を紹介させていただきますのでお気軽にお声がけください。
弊社所有のデモ機であればサンプル作成も常時受け付けております。
また、弊社にはプラズマ以外の処理装置も多数ございます。
合わせてご検討いただければ幸いです。
プラズマ処理をはじめ、各種表面処理装置を導入することで、脱プライマー・脱溶剤といった
作業環境や作業効率の改善、そして自然環境を配慮したモノづくりへの転換を図ることができます。
表面処理を導入し、SDGsの下記目標を達成しましょう。
3.すべての人に健康と福祉を
ー3.9:2030年までに、有害化学物質、並びに大気、水質及び土壌の汚染による死亡及び疾病の件数を大幅に減少させる。
8.働きがいも経済成長率も
ー8.2:高付加価値セクターや労働集約型セクターに重点を置くことなどにより、多様化、技術向上及びイノベーションを通じた高いレベルの経済生産性を達成する。
9.産業と技術革新の基盤をつろう
ー9.4:2030年までに、資源利用効率の向上とクリーン技術及び環境に配慮した技術・産業プロセスの導入拡大を通じたインフラ改良や産業改善により、持続可能性を向上させる。全ての国々は各国の能力に応じた取組を行う。
12.つくる責任 つかう責任
ー12.4:2020年までに、合意された国際的な枠組みに従い、製品ライフサイクルを通じ、環境上適正な化学物質や全ての廃棄物の管理を実現し、人の健康や環境への悪影響を最小化するため、化学物質や廃棄物の大気、水、土壌への放出を大幅に削減する。