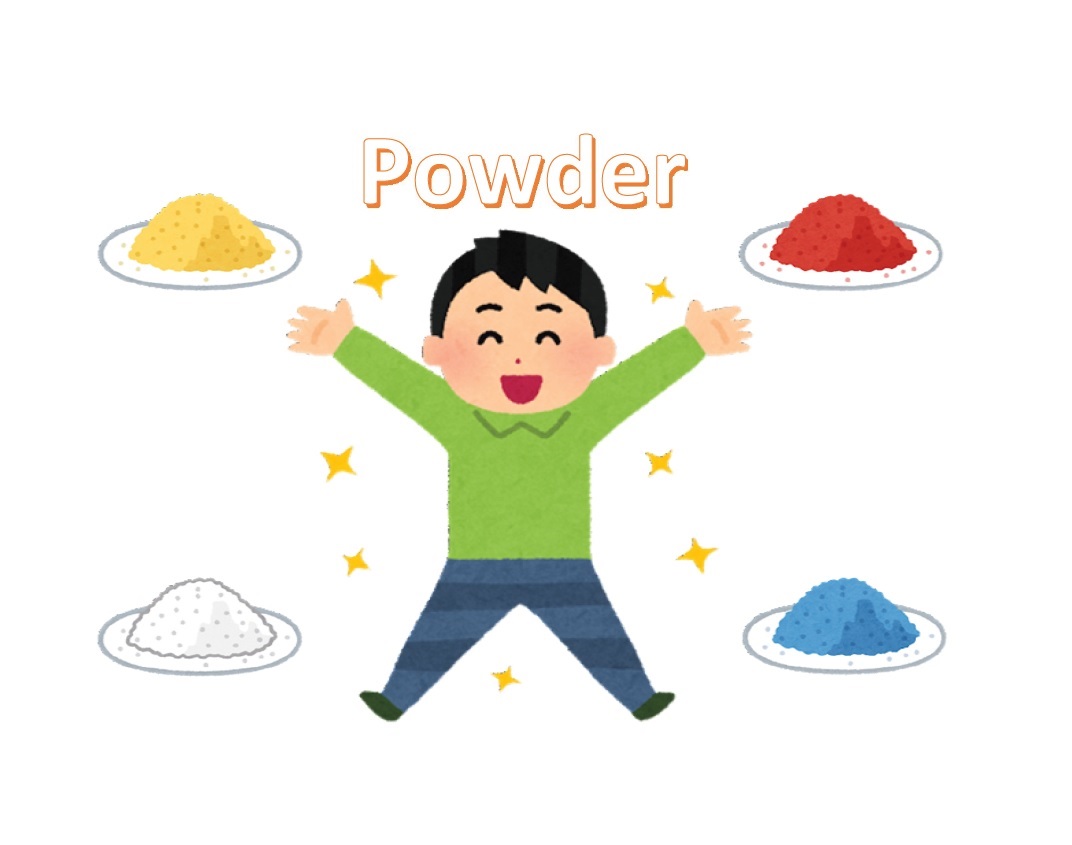
はじめに
接着や密着のための表面処理は、主にフィルムなどフラットな製品の表面を処理するために使われてきました。
その後技術発達やアプリケーションの多様化が進み、低圧下やスポットタイプのプラズマ処理・
フレーム処理機等により、三次元の製品表面にもプライマーレスで濡れ性向上・接着性能アップなどの
効果を付与することが可能になりました。
理論的には、どれだけ製品が大型化しても、既存の処理機の大型化やマルチ化(複数を同時使用)で
対応可能ですが、逆に小型化された場合はどうでしょうか?
表面処理に残された最後の分野がこの小型化された材料、大きさにより粉体や粉体などと呼ばれる「粉」です。
数ミリ程度の大きさから数ミクロンまで、「粉」と呼ばれる状態の材料をどのように処理をするのか。
ここまで一つ一つの材料が小さくなってくると、既存の処理方法をそのまま応用することが難しいのですが
弊社が扱う粉体用プラズマ処理機は、粉体状態にも親水化させることが可能です。
プラズマ処理とは
他ブログにて紹介しておりますが、プラズマとは、気体を電気や熱によって分子や電子を分離させた状態です。
この状態では原子や電子が非常に活性の高い状態を維持しているため、安定状態の分子と結合し
親水性の官能基を生成したり、表面上の有機物と反応し除去する効果があります。
詳しくは「表面処理とは」 または 「プラズマ処理とは」 をご覧ください。
粉体プラズマの特徴
弊社が取り扱うチェコのSurfaceTreat社製の粉体プラズマ処理機は、2.45GHzの真空マイクロ波(MW)の
プラズマを利用しています。
マイクロ波プラズマの特徴は、導体・絶縁体どちらの材料も処理ができる、温度がLFやRFといった
他の発信方式よりも低い等があります。
また、イオン密度が高いので、粉体処理には最適の処理方法です。
樹脂の粉や金属の粉、セラミックなど無機系の様々な粉が存在しています。
粉によっては処理時間が長くなり、粉の温度も上昇してしまいますが、イオン密度が高ければより短時間で
処理できるため、粉の処理にはマイクロ波が最適な選択肢となります。
なぜ真空プラズマなのか?
大気圧下でも粉へのプラズマ処理が可能ですが、真空で行う方式には大気圧に比べ以下のメリットがあります。
1:ガス消費量が抑えられる。
ー 大気圧では常に多量のガスを流し続ける必要がありますが、真空プラズマでは10-50pa程度に
保つだけの量で済むため、10-100分の1の量で抑えられます。
2:大容量化ができる。
ー 大型の真空プラズマ設備はすでに存在しており、メーカーも大型機の開発に成功しておりますが
大気圧では設備大型化に伴う付帯設備の設計なども発生するため、コスト面でみると非現実的です。
3:粉のハンドリングが容易。
ー 真空に引いてガスを投入、その後大気に戻すというプロセスは同じため、粉でも通常の真空プラズマと
同じように処理ができますが、大気圧では粉とガスの分離という問題が発生するため
粉の回収が大きな課題となります。
結局のところ、粉体用の処理装置の多くは、大気圧でもバッチ方式となってしまうため、
真空プラズマでバッチであるというマイナスのイメージがデメリットではなくなっています。
粉体プラズマの可能性と用途
粉を親水化することで様々なメリットがあります。
今まで表面処理を施して粉の接着性を改善すること自体あまり一般的ではなかったため
粉体向けの用途には大きな可能性があります。
今までできなかったことが、プラズマ処理によって実現するかもしれません。
粉のプラズマ処理で一般的な用途を簡単にご紹介します。
用途その1:分散性の向上
一般的な成形品と同様に、粉もプラズマ処理を施すことで親水化されます。
その粉を水と混ぜるとどうでしょうか?
撥水性の強いプラスチックでは比重により水の中で分離したまま沈殿、または浮いたままで攪拌しても
決して混ざることはありませんが、プラズマ処理をした粉は、混ぜることで水の中に拡散していきます。
もちろん溶けるわけではないので、時間と共に沈殿したり浮上したりし分離はしてしまいます。
粉自体を親水化させることで、分散剤を用いること無く水へ分散させることが出来るようになります。
分散剤を削減することにより、製造工程の簡素化やランニングコスト低減・管理の手間を省くことが可能です。
親水化による新たな用途開発だけではなく、既存工程の見直しなどにも寄与できます。
未処理(左) プラズマ処理済(右)
用途その2:接着性の向上
既に実用化されているアプリケーションで、プラズマ処理をした粉を使った回転成形があります。
回転成形とは、加熱した金型の内側へ粉を入れ、金型を回転させつつ金型を加熱することで、
粉同士を溶着させながら積層して製品の形にする成形方法です。
大型で少量多品種の部品に使用させる方法です。
(詳しくは回転成形の専門メーカー様のサイトをご参照ください。)
この粉をプラズマ処理をした粉に置き換えることで、成形面に親水性を保持した製品を作ることが出来ます。
未処理の粉、樹脂面と剥離している。
プラズマ処理を施した粉、樹脂面と接着している。
どのような粉が処理できるの?
基本的に粉の種類に制限はありませんが、極端に粒径が小さいもの、例えば1桁ミクロン前半や
ナノレベルの粒子、そして比重が軽い粒子は、処理に時間がかかったり処理プロセスの最中に
飛び散ってしまうリスクがあります。
材質に関しては樹脂(例えばポリエチレン)、金属(銅やアルミなど)からセラミックの粉まで
様々な粉の処理が可能です。
小さな粉をお考えの方はまずはご相談ください。
メーカーで受託加工をしている客先預かりの粉体
最後に
粉体の親水化、分散技術はカップリング剤を介して行われていました。
このカップリング剤の混ぜ方などはノウハウの塊で内製化するのが難しく
カップリング作業から納入までのリードタイムも生産工程管理のネックとなっていました。
しかしこのプラズマ処理なら、親水化処理も内製化することが出来、製造工程の上流から下流までの
流れスムースにコントロールすることがができます。
粉体のプラズマ処理を実現することで、生産効率の改善や、品質の安定化などといった付加価値も
得ることが出来ます。
粉体へのプラズマ処理は新しい技術です。
是非この技術を貴社の製品でお試しください。