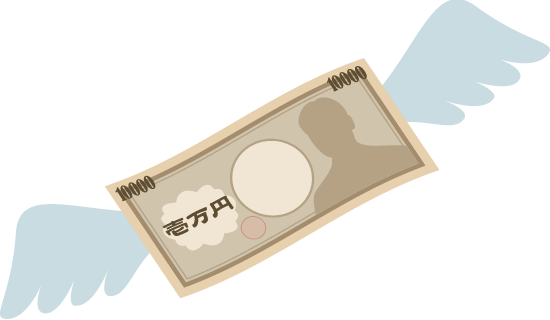
目 次
|| イオナイザの圧縮空気の電気代は”見える化”できる!
|| バー型イオナイザの圧縮空気の電気代 計算方法
例1)バー型イオナイザ 1台 バー幅1,000mmの場合
例2)クリーンブース25台で計50台のイオナイザを運用している場合。
例3)樹脂部品を成型後のコンベヤ搬送工程。20ラインで計100台 のイオナイザを運用している場合。
(※注1)
(※注2)
|| スマートイオン(エアフリー パルスDCイオナイザ)で工場の圧縮空気を節電できます
|| スマートイオン(エアフリー パルスDCイオナイザ)の主な用途
|| イオナイザの圧縮空気の電気代は”見える化”できる!
工場で使用している除電装置には、圧縮空気を接続して、イオンを広範囲に輸送するタイプの除電器があります。AC型・パルスAC型で典型的なスペックです。これらの除電器は、クリーンエアにイオンを載せて送風することで、基材の静電気を中和する効果がある一方、コンプレッサーの電気代がランニングコストとして発生するという一面があります。
バー型イオナイザのエアブローは、”エア漏れ”という視点で見ることも出来ます。除電バーからのエアブローを無くすことができれば、工場の圧縮空気の電気代を大きく削減することにつながります。
除電器のエアブローを見直すにしても、既存の除電器がどれ位の圧縮空気を使用して、ランニングコストがどれほどかかるものなのか、試算して”見える化”することが初めの一歩です。このページでは、バー型イオナイザの電気代の試算方法を説明していきます。
バー型イオナイザの圧縮空気の電気代 計算方法
” バー型イオナイザ1台が年間に消費する圧縮空気の電気代 ” を算出することが目的です。
試算の概要は、
①1分間での漏れ量(m3/min)⇒ ②年間の漏れ量(m3/年)⇒ ③除電バー1台が年間に消費する圧縮空気の電気代(円/年)
③を算出することが目的です。③除電バー1台が年間に消費する圧縮空気の電気代(円/年)=②年間の漏れ量(m3/年) x ④圧縮空気の単価(円/m3)(※注2)です。
②年間の漏れ量(m3/年)=①1分間での漏れ量(m3/min)x 60min/h x ⑤1年間の運転時間(h/年) です。
例1) バー型イオナイザ 1台 バー幅1,000mm 圧縮エア消費量は256L/min (0.3MPaで運転)の場合 (※注1)
①1分間での漏れ量(m3/min)は、256L/min x 0.001m3/L =0.256m3/min です。④圧縮空気の単価(円/m3)を2.3円/m3(※注2)、⑤1年間の運転時間を5,000時間とすると、
③除電バー1台が年間に消費する圧縮空気の電気代=①1分間での漏れ量(m3/min)x 60min/h x ⑤1年間の運転時間 x ④圧縮空気の単価(円/m3)=0.256m3/min x 60min/h x 5,000h x 2.3 円/m3 =176,640円
これが、バー幅1,000mm の送風型イオナイザ1台が1年間に消費する圧縮空気の電気代です。
例2)
立ち作業のクリーンブースで、樹脂部品を組み上げるアッセンブリ工程の例。
ブースの天井にバー型イオナイザ(バー幅 500mm)を2台設定しており、クリーンブース全25台で合計 25 x 2台 = 50台のイオナイザを運用しているとします。
バー型イオナイザ 50台 バー幅500mm 圧縮エア消費量は128L/min (0.3MPaで運転)の場合
①1分間での漏れ量(m3/min)は、128L/min x 0.001m3/L =0.128m3/min です。④圧縮空気の単価(円/m3)を2.3 円/m3(※注2)、⑤1年間の運転時間を5,000時間とすると、
③除電バー1台が年間に消費する圧縮空気の電気代=①1分間での漏れ量(m3/min)x 60min/h x ⑤1年間の運転時間 x ④圧縮空気の単価(円/m3)=0.128m3/min x 60min/h x 5,000h x 2.3 円/m3 =88,320円
台数が50台なので、88,320円 x 50=4,416,000円
これが、バー幅500mmの送風型イオナイザ50台が1年間に消費する圧縮空気の電気代です。
例3)
樹脂部品を成型後、コンベヤ搬送部で1ラインに付きバー型イオナイザ(バー幅 500mm)を5台設置しており、全20ラインで合計 20ライン x 5台 = 100台 のイオナイザを運用している場合。
バー型イオナイザ 100台 バー幅500mm 圧縮エア消費量は128L/min (0.3MPaで運転) とします。
①1分間での漏れ量(m3/min)は、128L/min x 0.001m3/L =0.128m3/min です。④圧縮空気の単価(円/m3)を2.3 円/m3(※注2)、⑤1年間の運転時間を5,500時間とすると、
③除電バー1台が年間に消費する圧縮空気の電気代=①1分間での漏れ量(m3/min)x 60min/h x ⑤1年間の運転時間 x ④圧縮空気の単価(円/m3)=0.128m3/min x 60min/h x 5,500h x 2.3 円/m3 =97,152円
台数が100台なので、97,152円 x 100=9,715,200円
これが、バー幅500mmの送風型イオナイザ100台が1年間に消費する圧縮空気の電気代です。
静電気除去バーは、クリーンエアをブローするために、多額のコストをかけて圧縮空気を使用しているのです。
~~~~~~~~~~~~~~~~~~~~~~~~~~~~~~~~~~~~~~~~~~
(※注1)
静電気除去バーの ノズル1穴当たりのエア消費量を約16.0L/min(0.3MPa)、 長さ1,000mm でノズル16穴の場合、 16穴 x 16.0L/min = 256L/min=0.256m3/min
1分間での漏れ量 0.256m3/min
年間の漏れ量 0.256m3/min=15.36m3/h x 5,000h/年=76,800m3/年
年間の損失コスト 76,800m3/年x2.3円/m3=176,640 円/年
(※注2)
④圧縮空気の単価(円/m3)の試算方法
圧縮空気の単価(円/m3)=[モーター出力(kW)x 電気料金の単価(円/kWh)] / [モーター効率(%)x 吐出空気量(m3/min)x 60min/h] です。
コンプレッサーのモーター出力37kW、吐出空気量6.3m3/min、モーター効率85%、電気料金単価20円/kWh とした場合、空気単価は
[37kW x 20円/kWh] / [85% x 6.3m3/min x 60min/h] =740円/h / 321.3m3/h =2.3 円/m3 です。上の例1、例2では、圧縮空気の単価を 2.3 (円/m3) としました。
この計算式では、⑥設備償却コスト(コンプレッサーを購入したときの費用)・⑦コンプレッサーの年間のメンテナンス費用、が反映されていません。⑥⑦を加味した圧縮空気の単価(円/m3)を計算する場合は、次のような方法があります。
圧縮空気の単価(円/m3)={[モーター出力(kW)x 電気料金の単価(円/kWh)x ⑤1年間の運転時間] + [⑥設備償却コスト] + [⑦コンプレッサーの年間のメンテナンス費用]} / [モーター効率(%)x 吐出空気量 (m3/min)x 60min/h x 1年間の運転時間(h/年)]
37kWのコンプレッサーの購入金額500万円、償却期間10年とすると、⑥コンプレッサーの1年当りの設備償却コストは、500万円÷10年=50万円/年 です。
コンプレッサーのメンテナンス費用は、シール交換・オイル交換・潤滑・保守など、年間20万円とすると、⑦コンプレッサーの年間のメンテナンス費用は、20万円です。1年間の運転時間を6,000(h/年)として、
これらを圧縮空気の単価に勘案して計算すると、
圧縮空気の単価(円/m3)= {[37kW x 20円/kWh x 6,000h/年] + [50万円/年] + [20万円/年]} / [85% X 6.3m3/min X 60min/h x 6,000h/年 ]
= {[4,440,000円/年] + [500,000円/年] + [200,000円/年]} / [1,927,800m3/年] = 2.67(円/m3)
スマートイオン(エアフリー パルスDCイオナイザ)で工場の圧縮空気使用量を削減できます!!
スマートイオン(エアフリー パルスDCイオナイザ)は、最新のパルスDCテクノロジーを結集して設計されたコンプレッサーフリーの除電装置です。クリーンエアは不要で、高いイオンバランスで広範囲を除電することができます。パルスDCの市場参入により、送風型静電気除去バーに代わる代替技術が存在することになります。
工場で使用される電力のうち、20~30%は、コンプレッサーの電力といわれています。コンプレッサーによる電気代を節電するためには、エア漏れを防ぐ・エア圧を下げる、のようなすぐに出来ることから、高効率な圧縮機にリプレースする・工場エアのフロー全体を効率化する、というような抜本的な視点から見直すこともあります。
送風型イオナイザによるエア漏れは、 スマートイオン(エアフリー パルスDCイオナイザ)に置き換えることで、簡単に防止することが出来ます。除電バーが消費する圧縮空気の電気代は、計画的に削減していくことが出来きます。
|| スマートイオン(エアフリー パルスDCイオナイザ)の主な用途
〇 フィルム
:コイルからも巻きだしで、剥離帯電による静電気を除電
:コイルへの巻取りで、巻き取る直前にフィルム両面を除電
:スリッターで裁断後に除電
:ロールtoロールに設置して、ロールとフィルム間の摩擦帯電・剥離帯電を防止
〇 シート
:シートと紙の張り合わせ後に除電
:シートを除電してから上からチャック
〇 金属箔
:アルミ箔・銅箔の上にペースト(活物質)塗工後、ロールtoロールプロセスで除電
〇 射出成型
:成形トラブル・成形不良防止のため、金型の中を除電
:成型品をコンベヤ搬送する工程で部品の静電気を除電
〇 ガラス
:板ガラス加工工程で除電(ロール搬送工程)
:ガラス繊維製造工程で除電(整経・整織・表面処理など)
〇 印刷
:シルクスクリーン印刷機の前にパルスDCイオナイザを設置して、印刷不良対策
(インクの飛び散り防止、版の汚染防止)
:デジタル印刷機のロール給紙部にパルスDCイオナイザを設置して、印刷不良対策
〇 ファイバー
〇 クリーン環境
:クリーンルームの中を浮遊している小さなホコリの静電気を除去して、製品への付着防止
:クリーンブース・クリーンベンチの天板にパルスDCイオナイザを設置して、基材へのホコリやゴミ付着を防止
関 連 情 報
スマートイオン(エアフリー パルスDCイオナイザ)の詳細をみる
エアフリー(無風)除電技術を工場の低炭素化に活かす!をみる
製造現場の静電気 | 基礎から学び不良低減につなげよう! をみる
なぜゴミや異物の問題がなくならないのかをみる