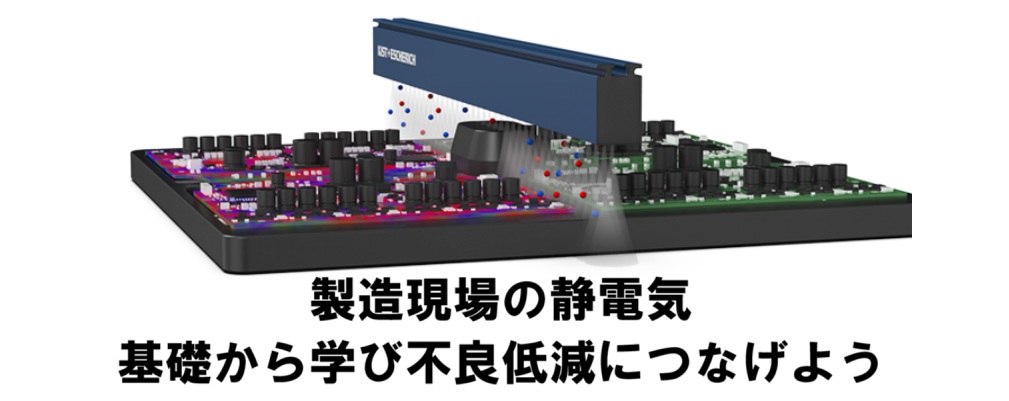
製造現場での静電気について基礎からまとめました。
|静電気が発生する原因|静電気対策の方法|静電気対策装置・除電装置|静電気による異物・コンタミ吸着と対策|異物除去|除塵|を考えるためのページです。
目次
|| 身近なところで起きている静電気
|| 物質を構成している原子や分子から静電気を考える。
|| 静電気の発生は、接触に起因しています
|| 物質が静電気を帯びる その他の要因
|| 静電気の強さ及び極性(プラス/マイナス)に影響を及ぼす要因
|| 静電気を測定する方法
|| 放電と静電気除去
|| 静電気を除去する方法
a)自己放電型
b)放射線による除電方法
c)電圧印加型(イオナイザ)
d)静電気除去液
e)湿度管理
|| AC型、パルスAC型、DC型、パルスDC型の特徴
a) AC型・パルスAC型
b) DC型・パルスDC型
c) 高周波AC型
|| 最新のパルスDCテクノロジー
|| エアフリー除電技術を工場の低炭素化に活かす
|| 剥離帯電・摩擦帯電を解消する方法:非接触浮上・非接触吸着
|| 静電気のトラブル|事例と対策
a) 静電気でゴミ・異物が付着する問題→事例と対策
組立・アッセンブリ | 塗装 | ラミネート | ||
ロールtoロール | トレー | 印刷 | ||
スクリーン印刷 | スリッター | 電池 電極 | ||
Oリング | ストレッチフィルム | カレンダーロール | ||
光ファイバー | フィルム巻取り | フィルム巻き出し |
射出成型 | 二枚取り | 樹脂ホース・パイプ |
グリーンシート | パーツフィーダー | スクリーン印刷 |
コンベヤ | オフセット印刷・輪転機 | スリッター |
充填・製袋 | 縦型包装機 | クリーンルーム |
フィルムの巻取り・巻き出し | スライサー | 静電気破壊 |
|| 静電気を制御して、生産を効率化させているプロセスもあります
材料分別 | フィルム・紙 蛇行防止 | ターレット巻取り機 |
貼り合わせ | 粉体静電塗装 | タルク塗布装置 |
|| 粉塵爆発と爆発性粉塵
|| 危険区域での放電
|| 産業用途での静電気除去・除塵について
|| 生産環境での異物の量
|| 除電器・イオナイザの種類と選び方
関連情報
|| ドライクリーナー・洗浄装置の種類と選び方
|| なぜゴミや異物の問題がなくならないのか
NEW! エアーフリー除電技術がカーボンニュートラルに貢献できる理由
NEW! エアーフリー除電技術は工場のSDGsへの取り組みの切り札!
|| 身近なところで起きている静電気
静電気は直接観察することができませんがその効果によって気づくことができる自然現象です。静電気は日常生活の中でも身近なところで発生しています。例えば、脱衣の時パチパチ音がする現象、ラップを巻いていくと静電気でくっついてしまう現象、雨雲からの雷、パソコンの画面にホコリが付着する現象、これらは全て静電気による現象で、電荷のバランスが崩れることにより力が生じたり放電が起きたりするのです。
|| 物質を構成している原子や分子から静電気を考える。
原子は、プラスの電荷を持つ陽子とマイナスの電荷を持つ電子で構成されています。静電気を理解する上で重要なことは、電荷の割合です。
A)電子の数=陽子の数 → 中性
B)電子の数>陽子の数 → マイナスに帯電
C)電子の数<陽子の数 → プラスに帯電
同様に、原子で構成されている物質のキャリアの割合も電荷に影響を及ぼします。マイナスのキャリアが多いと物質はマイナスに帯電します。逆にプラスのキャリアが多いと物質はプラスに帯電します。
|| 静電気の発生は、接触に起因しています
1) 二つの物質が接触していると、それぞれの物質を構成している原子は、接触面で極めて近づくことになります(数ナノメートル)。表面の原子から電子はもう一方の物質へ移動できるようになります。移動方向と強さは物質の物理的性質によります(電子伝達)。
2) もし、二つの物質が離れると、移動した電子は片方の物質に残ることになります。これにより一方の物質に電子が偏り(マイナスに帯電)、もう一方の物質は電子が減少(プラスに帯電)することになります。
この現象は、導電性物質でも絶縁体にも起こります。
また、この現象は固体だけでなく、液体やガス状物質でも同様に生じます。
|| 物質が静電気を帯びる その他の要因
□ 強い電場(静電誘導)
□ 物質の変形・冷却
□ 他の物質との摩擦(摩擦帯電)
|| 静電気の強さ及び極性(プラス/マイナス)に影響を及ぼす要因
□ 材質
□ 周辺環境(湿度、温度)
□ 表面特性(粗さ、など)
□ 頻度:接触・剥離を繰り返すプロセスでは部材の静電気が強くなっていきます
□ 剥離の仕方:例えば、部材の剥離速度が速いほど、より強く静電気を帯びます
|| 静電気を測定する方法
静電気は電場(電界)を形成します。電場の磁束線は、負から正の向きに流れます。帯電した物質が、電場の領域に侵入すると、その物質には力が働きます。髪を洗ったり、櫛でとかすと髪の毛が逆立つ現象も、この力で説明することが出来ます。
これは、導体の電子に作用している力で、特別な測定器で測定することが出来ます。これが静電気測定器です(静電気測定器エルフィ Iをみる)。通常、電場の単位 V/m で測定します。静電気測定器は、帯電物と非接触で測定することができ、帯電物の材質に関係なく測定できるので、多くの製造現場で使われている測定器です。静電気を帯びた物体の表面には電界が発生しています。電界の場の強さを、測定可能な量に換算して測定値を V/m で表示します。
|| 放電と静電気除去
偏在している電荷は、均衡をとろうとする性質があります。
□金属のような導電性物質が帯電している場合、負電荷はアースに接続した電極に流れます。
□気体または液体中の帯電した分子は、帯電した物質の表面に接触することで、不足している電荷を供給する 或いは 電荷を吸収することにつながります。これにより表面の静電気が中和します。
□電荷の中和は、物質内でも起こり得る現象です。例えば、異なる電荷が偏在している物質内で電気抵抗が有限な場合です。
|| 静電気を除去する方法
a)自己放電型:
針状でアースした導体(イオナイザー)は、帯電した物体の近傍では、周囲の空気中の分子をイオン化することが出来ます。この空気中のイオンは帯電物の表面を中和することができます。針状の電極と帯電した表面の間の電場によりイオンは輸送されます。この主のイオナイザーとして、除電紐・除電ブラシなどがあります。非常に効率的に電位を低減させることができる一方、針状の電極と帯電した物質間の電位差によるコロナ放電現象なので、電位差が小さいと静電気を中和することは出来なくなります。
b)放射線による除電方法:
イオナイザからの放射線(軟X線、α線、紫外線など)が雰囲気ガス中の分子を電離して、プラスイオン・マイナスイオンが生成します。そして、帯電物の静電気の極性と逆の電荷が表面に引き寄せられて、表面の電位を中和する原理になっています。
電離とは、電磁波や放射線によって、原子が電子を放出することです。マイナス電子を放出した原子がプラスイオン、マイナス電子を吸収した原理がマイナスイオンになるので、放射線によってプラスイオン・マイナスイオンが生成されるのです。
放射線による静電気除去は、空気中での除電だけでなく、窒素など不活性ガス雰囲気下での除電や、紫外線タイプの場合、減圧下での除電という独特な用途もあります。この除電方法は、放射性物質の取扱いや安全上の問題のため、特別な用途に限って用いられています。放射線取扱のため所轄官庁への届出、運転中に放射させる放射線を遮へいする設備、ベリリウムウィンドウの取扱・排気方法、X線チューブ等 消耗品の準備など、導入前に設備管理の確認が重要です。
c)電圧印加型(イオナイザ):
針状の電極に高電圧を印加することで強い電場を形成します。この電場は空気中の分子を電離してイオン化し、帯電した表面へ放電されることで静電気を中和する効果があります。空気中の分子をイオン化する力は、帯電物の電荷とは無関係で、自己放電型と比べ、表面の静電気をゼロ近くまで中和することができます。電圧印加型には、交流(AC)除電装置、直流(DC)除電装置、パルスDC除電装置などがあります。
d)静電気除去液:強い静電気は、静電気除去液(static inhibitor)と呼ばれる溶液で除去することができます。帯電防止剤という呼称もあり、主に水や溶剤で希釈した界面活性剤が使われています。界面活性剤は、親水基と親油基を併せ持つ分子構造をしています。静電気除去液を基材に塗工すると、界面活性剤の親水基が周辺の水分を取り込み表面に薄い導電性の膜を形成し、静電気を防止することができます。
界面活性剤を含有した静電気除去液を工場で使用する場合には、工場内の湿度が静電気防止効果に影響を及ぼす要因になります。市場には、界面活性剤を使用しない静電気除去液も存在します。
どのような静電気除去液を使用する場合でも、溶液と基材の反応性がないことを確認した上で、適用する必要があります。
e)湿度管理:夏場よりも冬場の方が、静電気の問題が起こりやすくなると聞いたことはありませんか?これも工場内の湿度に起因しています。湿度が高いと物質の表面は水分に覆われ、表面の電荷の漏洩率が高くなり静電気は拡散されやすくなると言われています。工場の湿度を管理する事により、静電気対策する施策があります。湿度は単に高ければ良いわけではありません。湿度が高すぎると生産設備を錆させる問題になり、食品工場では過剰な湿気でカビが発生すると重大な問題になります。適切なレンジ内に湿度を保持して湿度管理システムを運用する必要があります。
メリットは、工場内の湿度を均質に管理することにより静電気対策につながり歩留まり低減効果がある・乾燥による細菌の繁殖の対策にも効果がある・乾燥対策になるので、作業者の皮膚の保湿により作業環境が向上することが挙げられます。
デメリットは、水道水を使うと、配管が錆で腐食したりカルキで詰まる問題がある・純水やイオン水を使うとランニングコストが高くなる・水質管理のため、フィルター・活性炭・カートリッジが消耗品として発生する。除電の即効性は低いので、システムをONにしてから物質の静電気が低下するまである程度時間を要する・システム全体の初期投資が高いことが挙げられます。
|| AC型、パルスAC型、DC型、パルスDC型の特徴
電圧印加型除電器は、静電気を積極的に中和する設備として多くの工場に導入されています。大きくは、交流(AC)型と直流(DC)に大別でき、その中でも AC型、パルスAC型、DC型、パルスDC型、ダブルDC型が存在します。それぞれの特徴をまとめておきます。
a) AC型・パルスAC型
ACタイプの除電器は、トランスで5kV~8kVの高電圧に変換しています。針状電極の先端で印加電圧によりプラスマイナスイオンが周波数(50または60Hz)に同期して交互に生成します。AC型は、近距離での除電に適しており、帯電物から20mm~50mm離して設置して運用します。無風で近距離除電用途に特化したAC型除電器は、導入コストが低く 多くの製造現場で使用されています。
放電針で生じたイオンを気流に乗せて、より遠くまで輸送する方法があります。そのため、AC型除電器にファンを搭載させたり、またパルスAC型除電バーの放電電極からクリーンエア放射口を搭載したモデルが市場に存在します。AC型・パルスAC型は、いづれも有効除電エリアを広くするためには、気流やクリーンエアが必ず必要になります。これは、下記の直流(DC)静電気除去装置との大きな違いです。
気流でイオンを輸送する利点は、イオンを遠くまで輸送できることで、成型品のような表面が凸凹した立体物を除電する用途にも活用できる可能性が広がります。クリーンエアまたは窒素ガス・アルゴンガスを供給する除電器の場合は、機種を選定する際には、エア・ガスの消費量と運転圧力を確認して、ランニングコストを試算する必要があります。また、クリーンエアまたは窒素ガスどちらを使用する場合でも、除電器に投入する圧力はシビアに管理する必要があります。用途により、エア圧が強すぎると逆帯電の原因になる可能性があり、逆にエア圧が弱すぎると基材まで十分なイオンを供給できず静電気を中和できていないことが起こりえます。(バー型イオナイザの圧縮空気の電気代 試算方法をみる)
b) DC型・パルスDC型
DC型は、除電器にプラス用電源とマイナス用電源を内蔵し、それぞれ別々の放電電極からイオンを生成する方式です。プラスを放電する電極と、マイナスを放電する電極が分かれています。DC除電器のメリットは、ACタイプの除電器よりもイオンを遠くまで無風で輸送することが出来ることです。除電器から200mm以上のミドルレンジからロングレンジまでを無風で除電するために運用します。AC除電器では、プラスからマイナスイオンに切り替わるときに、イオンが生成していない休止時間がありますが、パルスDC除電器では、イオンの極性が切り替わるタイミングでも休止時間がありません。
パルスではないDC型は、放電針で生成したプラスとマイナスのイオンが基材へ到達する途中に再結合(プラスマイナス=ゼロ)する可能性があります。つまり、イオンが基材へ届く前にイオンが消えてしまうので、基材の静電気を除電できないことになります。除電器の設計段階で再結合を考慮する必要があり、また除電器を現場に設置する時に再結合せずにイオンを基材まで輸送できるよう配慮して敷設する必要があります。
パルスDCは、プラスイオンとマイナスイオンを交互(パルス)に放射することで再結合を防いでイオンを遠くまで輸送する新しい技術です。これによりファンやクリーンエアを使用せず、イオンを遠くまで輸送することが可能になります。パルスDC除電器の中には、除電器から1500mm先まで無風でイオンを長距離輸送できるモデルも存在します。除電器のユーティリティーは電源操作だけなので、運転や保守管理も簡単になります。また非送風型は、ランニングコストが極めて低いのが特徴です。
パルスDC除電器の典型的な用途は、エアーブローを嫌う用途での静電気対策です。
例えば、クリーン環境での静電気対策が挙げられます。クリーンルームでは多くの場合、室内でエアーブローすると、小さなホコリや微粒子を飛散させるので、エアーガンのように気流を生成する設備は使用を控える傾向があります。
また、ガラス繊維・不織布・枚葉シート・枚葉フィルムを除電する用途も、エアーブローを当てると 繊維がケバ立つ・軽量シートが動いてしまう等の問題があるため、エアーブローしない除電器・イオナイザのニーズがあります。
こうした用途では、現場に導入する除電器を選定する段階で、エアーブロー型・送風型では無い除電器から選定していきます。パルスDCはこのようなマーケットで重要な選択肢となっています。
c)高周波AC型
上記(a)で述べた低周波型AC除電器が50Hz~60Hzの周波数であるのに対し、高周波ACイオナイザは65kHz~70kHzの周波数帯で運転する除電器です。周波数は、放電針に印加する電圧がプラスとマイナスで切り替えする頻度を表しています。印加電圧を高周波にするということは、プラスイオンとマイナスイオンを放出する切り替え頻度が早くなり、イオンバランスが向上することにつながります。一方、高周波AC型は出力電圧が低いのも特徴です。AC型、DC型が7~8kV、パルスDCは8kV~33kVの印加電圧を適用しているのに対し、高周波AC型は2kV弱の電圧を印加しています。印加電圧の強弱は、イオン生成量を表しています。
高周波ACに適した用途は、小さな静電気量にも敏感な基材の除電です。例えば、ICチップ・半導体ウェハ・液晶部品の除電です。これらの用途は、わずかな静電気でも静電気破壊・絶縁破壊が問題になる可能性があるので、イオンバランスの良い高周波AC型が適した用途になります。
スポット高周波ACイオナイザ SI プレシジョンをみる
バー型高周波ACイオナイザ プレシジョンバーをみる
|| 最新のパルスDCテクノロジー
一般的な直流型除電器は、プラスイオンを放射する放電針とマイナスイオンを放射する放電針が分かれており、それぞれ電源から高圧を印加することでイオンを基材へ放射します。しかし、イオンが基材へ到達する前に、プラスイオンとマイナスイオンが互いに引き寄せられることがあります。これを再結合といいます。再結合が起こると、十分なイオンを基材へ輸送することができず、基材の静電気を中和できない原因になります。これが旧来のDC除電器でした。
再結合を防止して、かつ均質なイオンバランスでイオンを無風で基材へ輸送するべく開発されたのが、パルスDC方式です。
パルスDCは、除電方式が様々存在する中で、新しい部類の除電技術です。ヨーロッパでは、日本よりも工場現場への普及が進んでいるといわれています。パルスDC除電器の製造会社も海外勢が中心です。
パルスDC型の静電気除去装置では、針状電極は直流パルスの高電圧で印加されます。出力電圧は7kVから、最大33kVの機種も存在します。AC型・パルスAC型では出力電圧が5~8kVであることを考えると、パルスDCは、イオンの供給量が豊富で、除電能力が強化されていることが分かります。スマートイオン(エアフリー パルスDCイオナイザ)の場合、全ての機種で針状電極への印加電圧は抵抗で抑制しており、電流値を低くコントロールし、運転中に作業者が放電針に触れても人体に危険が及ぶことは無く、高い安全性を有しています。
パルスDC型の最大の功績は、ファンやコンプレッサーエアが不要で、イオンを広範囲に無風で輸送する技術を確立したことです。この特徴により様々なメリットが生まれました。クリーン環境の用途では、パルスDC除電器は、気流を生じることがないので、環境中に舞っている微細な塵埃・パーティクル・不純物を飛散させることがありません。クリーンルームの設計気流をかき乱すことなく、室内の清浄度を保持しながら、高い除電能力で、基材表面の静電気を除電します。除電能力が高いので、除電の即効性が高いのもパルスDCの特徴の一つです。
また、枚葉樹脂シート・フィルムのような、エアーブローを当てたくない軽量基材に対しても、吹き飛ばすことなく 静電気をしっかり除電する事ができます。
パルスDCイオナイザにより、エアーブローに伴う問題を解消して、静電気対策することができます。
|| エアフリーパルスDCイオナイザを工場の低炭素化に活かす
前章(AC型、パルスAC型、DC型、パルスDC型の特徴)で、バー型イオナイザが、エアーブロー・除電ブローの動力源に圧縮空気(コンプレッサー)を使用していることを説明しました。
圧縮機を使用してエアーブローするということは、電気代の負担が大きいことは想像できますが、CO2排出増加につながっているということをご存じでしょうか?
圧縮機の使用は、多大な電力消費につながります。
工場の電気は、電力会社が発電所から作り出しています。発電所には、原子力発電、LNG火力、石炭火力、石油火力、再生可能エネルギー(太陽光発電、水力、風力発電)があります。それぞれの電源を組み合わせて電気を作り、工場に届けています。そして、発電所は、電気を作る過程で二酸化炭素を排出しています。
つまり、エア式バー型イオナイザは、動力源の圧縮機を使用することにより、多大な電力を消費します。それが発電所の二酸化炭素(CO2)排出につながっているのです。
しかし、エアーブロータイプのバー型プイオナイザを、スマートイオン(エアフリー パルスDCイオナイザ)のような、エアフリー除電器に置き換えることができれば、圧縮機(コンプレッサー)の消費電力を低減することができるので、CO2排出削減することができるのではないでしょうか。
スマートイオン(エアフリー パルスDCイオナイザ)のように、エア式バータイプイオナイザと同等、あるいはそれ以上の除電能力を有するエアフリー除電技術は市場に存在しています。工場で、エアフリー除電器のテストをして条件確認を行い、除電能力に問題が無ければ、初期費用・ランニングコストを加味してリプレースを検討することができます。イオナイザという大量のエア漏れを無くしていくことができれば、コンプレッサー(圧縮機)が消費する電力使用量削減につながり、発電所のCO2排出を低減することになるはずです。これが、エアフリーパルスDCイオナイザで工場の低炭素化を推進できる理由です。
このたび、エアーフリー除電技術を活用して、工場のCO2排出量を削減する方法を考えるための新しいサイトを作りました。
日本の工場では、たくさんのエアー式バー型イオナイザが使用されています。エアー式イオナイザをエアーフリー パルスDCイオナイザに置き換えることは、単にコンプレッサーの電気代の節約につながるだけではなく、排出CO2削減に活かすことができる という一歩踏み込んだ視点です。
エアフリー除電技術を工場の低炭素化に活かす!で詳しく説明しています
その他、関連サイト:
エアーフリー除電技術がカーボンニュートラルに貢献できる理由
エアーフリー除電技術は工場のSDGsへの取り組みの切り札!
|| 剥離帯電・摩擦帯電を解消する方法:非接触浮上・非接触吸着技術
冒頭で、静電気の発生は”接触”に起因していると記述しました。
工場で生産している製品は、いろいろな物質と「接触」を繰り返して作られています。例えば、製品をロボットハンドでピックアップする工程では、ハンドと製品が接触し、離れます。また、ガイドロール・ローラーコンベヤでガラス基板を搬送する工程では、製品がロールと接触・剥離を繰り返して、搬送されています。製造現場のいろいろな場面で、製品と物質が「接触」する機会があります。そして、それが静電気が発生する原因になっています。
そもそも、製品との接触を回避することができれば、接触に起因する静電気発生を抑制することができるのではないでしょうか?
実際に、物質を非接触でピックアップすることにより、静電気の発生を抑制する新たな施策があります。基材を非接触で取り扱うことができれば、剥離帯電・摩擦帯電・圧着帯電に起因する静電気発生源を無くすことができるので、帯電防止につながるという視点です。
非接触 超音波 浮上・非接触 超音波装置は、ガラス基板・パネル・ウェーハ・ICチップに触れずに非接触で浮上させたり、非接触で吸着する技術です。製造元は、ZS-Handling GmbH (日本総代理店:ケー・ブラッシュ商会)です。振動板と基板の間にスクイーズ膜効果で空気膜を生成して浮上させる原理です。非接触で浮上中に周辺にエアーブローによる気流を発生させることもないクリーンな搬送技術です。超音波を非接触浮上・非接触吸着に応用した斬新な技術ですが、技術は日進月歩で進化しており 半導体業界・電子部品業界では、工場の生産設備として導入が始まっております。日本では、まだ普及の初期の段階ですが、欧米、韓国・台湾が設備投資に積極的です。超音波による非接触搬送技術は、すでに生産現場に適用できる再現性・安定性に到達しています。非接触搬送技術の運用ノウハウを製造現場に取り込むことにより、「接触」に起因する静電気の防止・「接触」による異物転写を防止することにつながります。
◆非接触浮上・非接触吸着技術のポイント
・「非接触」なので接触に起因する静電気発生を回避する
・「非接触」なので接触に起因するゴミ・異物・コンタミが転写するリスクを回避する
・「非接触」なので接触に起因する擦り傷・ダメージを回避する
◆超音波 非接触浮上・非接触吸着の用途:
ICチップ・ダイ | 枚葉フィルム | |
ウェーハ | 枚葉シート | |
レンズ | ガラス基板 | |
フラットパネル (FPD) |
リチウムイオン電池 電極・極板 | |
a) 静電気でゴミ・異物が付着する問題→事例と対策:
帯電したゴミ・ホコリ・ダスト・塵埃・製造現場で発塵した微粒子は、反対の極性の電荷や中性の表面に引き寄せられ、付着する原因になります。これにより、後工程で部材の品質を損なう原因となる他、ダウンタイム増加・生産停止・不良率増加等の原因につながる恐れがあります。
<組立・アッセンブリ> 樹脂成形部品を組立(アッセンブリ)する前に、クリーンブース内での立ち作業で清掃する工程。ブース内にイオナイザーを設置して、エアーガンで清掃作業することがあります。エアーガンで清掃しても効果が分かりにくく、逆に部材の静電気により浮遊塵埃・樹脂カス・ホコリ・バリなどを再付着させてしまう。
(プラスチック部品の付着異物対策をみる)
<塗装> 塗装工程で、樹脂部品を塗装する前にエアーガンで人手で清掃している。室内は、外部からの汚染物質が進入するのを防ぐために陽圧にしているが、エアガンで吹き飛ばしたパーティクルは静電気を帯びた樹脂部品に再付着する可能性は残ります。部品に異物が付着したまま塗装すると、重大な塗装不良(ブツ・ケバ)の原因になります。これが、歩留まり低減や塗料を無駄に消費することにつながっている。
(スプレー塗装工程での異物対策をみる)
<ラミネート> 2種類の樹脂製品(フィルムとシート、箔と樹脂製品など)をラミネートする工程では、貼り合わせる面に異物が付着していると、貼り合わせ後に外観不良・密着不良の原因になります。
<ロールtoロール> フィルム製造現場では、ロールトゥロールで走行しているフィルムは、ガイドロールとの接触・剥離を繰り返して走行することにより、静電気を強く帯びています。環境を漂っている粒子・ホコリ・ゴミを静電気で引き寄せて、表面に付着する原因になります。異物を付着させたまま巻き取ってしまうと、次工程または納品先でクレームにつながる恐れがあります。
(封止用フィルム製造工程で付着異物対策をみる)
(スリットカスを除去する3つの方法|切粉の問題はこれで解決!をみる)
(包装用フィルムの除電・除塵対策をみる)
(非接触ガイドロールで不良対策・静電気対策をみる)
(巻取ロールの静電気を効率よく除電する方法をみる)
(巻出ロールの静電気を効率よく除電する方法をみる)
<トレー> トレーの表面には、表面の静電気により工場ダスト、紙粉、体毛、異物、パーティクルが付着することがあります。トレーは部品を入れるための容器です。トレーに異物が付着すると、トレーに部品を積載させた時に転写して部品に付着する原因となり、後工程で様々な問題を引き起こし、歩留まりの低下や客先からのクレームの原因になります。
(3Dクリーナータイフンクリーンをみる)
(除塵ピストル|樹脂トレイの異物除去|吸引+パルスエアーブロー+除電+ブラシ)
<印刷> ゴミ・ホコリ・小さな異物が、被印刷物(フィルム・紙)に静電気で付着することがあります。その上から印刷することで印刷不良になる事があります。
ラベル印刷・オフセット印刷・輪転機・インクジェットプリンターなど、工場の印刷工程で起こりうる問題です。
(オフセット印刷で紙の静電気対策をみる)
(スクリーン印刷で樹脂フィルム・紙の静電気対策をみる)
(商業用デジタル印刷機で静電気対策をみる)
<スクリーン印刷> スクリーン印刷では、被印刷物が静電気を帯びていると、静電気自体が問題を引き起こす原因になります。
〇 静電気を帯びた樹脂シートに印刷すると、インクが飛び散る
〇 インクが版に飛び散ってしまう
〇 エアブロー式のイオナイザを使うとインクが乾いて印刷不良の原因になる。
〇 除電ブロー式のイオナイザを使うと樹脂シートが動いてしまう。
このようなケースでは、除電ブローしないパルスDCイオナイザを設置すると、印刷不良対策に絶大な効果を発揮します。
(スクリーン印刷前に印刷不良対策をみる)
(スクリーン印刷で樹脂フィルム・紙の静電気対策をみる)
<スリッター>スリット加工の工程では、ガイドロール部とウェブの接触により、剥離帯電が起こり、ウェブは静電気を帯びていきます。カッター部でウェブは長さ方向に切断されます。スリット時にスリットカスという呼称のパーティクルが発塵することがあります。ウェブが帯電していると、スリットカスは静電気の力でウェブの表裏や端面に付着していきます。静電気やスリットカスは、後工程や納品先の現場で問題を引き起こす原因となるので、除電対策を検討する必要があります。
(スリットカスを除去する3つの方法|切粉の問題はこれで解決!をみる)
(エッジのスリッター切粉を除電ブロー+吸引除去するクリーナーをみる)
写真:スリッター丸刃でフィルム切断 強い静電気で切カスが付着 スマートイオンでしっかり除電
<電池 電極> リチウムイオン二次電池の電極材製造工程では、金属系異物の付着が問題になることがあります。正極材は、アルミ箔の上にペースト状の電極材料(活物質溶液)を塗工、負極材は、銅箔の上に、電極材料(活物質溶液)を塗工して作られています。ロールtoロールプロセスで、工程間で発塵した金属異物(アルミ系・SUS系・鉄系)が浮遊して、電極材に付着することがあります。電極材のように基材が金属、浮遊異物が金属というケースでも、静電誘導により表面に電荷が移動して、静電気の力で異物が付着する問題が生じるのです。
(リチウムイオン二次電池製造工程での異物対策をみる)
(電極・極板の金属異物除去で実績多数!非接触式スタティックエアをみる)
<Oリング> 組立工程では、大量のOリングを用意して、製品に組み込んでいくプロセスがあります。
小さなOリングは、振動コンベヤで搬送されるときに、互いに擦れあい、静電気を帯びています。静電気は、生産環境中に浮遊しているゴミやホコリを引き寄せて表面に付着させていきます。Oリングに、ホコリ・ゴミ・切削屑・金属粉などが付着していると、製品に取り付けて組み込んだあとにトラブルにつながる恐れがあります。
例えば、Oリングに小さなホコリが付着したまま、配管接続部に取り付けてシールすると、小さな隙間がリーク源になり、シール不良につながる原因になります。
このようなトラブルを防ぐために、組立工程・アッセンブリ工程で使用する個々のOリングはきれいに清掃して、付着異物を除去する必要があります。
(大量のOリングをまとめてきれいにするクリーナーをみる)
<ストレッチフィルム> 出荷前に、パレットに積んだダンボール・貨物をストレッチフィルムで ぐるぐる巻く 作業があります。ストレッチフィルムを巻き付ける時に 周辺に浮遊しているゴミやホコリをくっつけて、ゴミ・ホコリまでフィルムで巻付けてしまうことがあり、これが問題につながることがあります。
(ストレッチフィルム包装機の静電気対策)
<カレンダーロール>製紙工程のカレンダー加工では、何本もの金属ロールと弾性ロールの間へ紙を通してプレスします。静電気を帯びたロールは、生産環境中に浮遊しているゴミ・ホコリ・繊維クズ・紙粉を吸着して、ロールを汚染する原因になります。
(製紙工程でカレンダーロールの静電気対策)
<光ファイバー>光ファイバー製造工程で、ファイバーを巻取り装置(スプーラー)で巻き取る工程があります。スプールで巻いたファイバーが静電気を帯びると、クリーン環境でも 室内を浮遊している微小なゴミ・ホコリ・繊維クズを引き寄せて表面にくっつけることがあります。こうした付着異物も巻き取る時にファイバーと擦れ合うことで、傷の原因になります。
(エアーフリー除電技術で光ファイバーの静電気対策)
<フィルム巻取り>ロールtoロール生産工程で、製造加工した紙・フィルムをロール状に巻取っていく工程があります。紙やフィルムは、巻取るとロールの中に静電気を蓄積していきます。ロールの静電気は、作業環境の悪化、ゴミ・ホコリを静電気で吸着してしまう問題や、次工程で巻出す時に、強く帯電した紙・フィルムが悪さを引き起こす可能性があります。
(巻取りロールの静電気を効率良く除電する方法)
<フィルム巻き出し>ロールtoロール生産工程で、製造加工した紙・フィルムをロールから巻き出す工程があります。紙やフィルムは、巻き出すと、剥離帯電により強い静電気が発生します。静電気は、作業環境の悪化、ゴミ・ホコリを静電気で吸着して次工程に持ち込んでしまうなどの問題につながります。
(巻出ロールの静電気を効率良く除電する方法)
b) 静電気でくっつく問題→事例と対策
静電気を帯びた物質同士はお互いに引き寄せ合ったり、機械部品にくっついたりすることで問題を起すことがあります。
射出成形機でプラスチック部品を金型で成形する現場では、金型を開いて部品を取り出すプロセスに静電気によるトラブルの原因が潜んでいます。開いた金型から部品を吸着パッドで取り出すときに部品が静電気で突き出しピンや金型内に貼り付いて取れ出せない問題が生じることがあります。これは、成形不良の増加や、警報で成形機が停止した場合にはメンテナンス中のダウンタイム増加につながります。
(プラスチック部品の成形工程で静電気対策をみる)
<二枚取り>
シートを1枚1枚載せていく工程で、シートを保持する治具やチャックに静電気でシートがくっついて離れなくなることがあり、ライン停止の原因になります。
(重ねた樹脂シートを除電して一枚づつ剥離をみる)
(エアーソード|重ねたウェーハを1枚づつ分離しますをみる)
<樹脂ホース・パイプ>
ペレットや粉をホースで配送していると、材料やホースが静電気を帯び、配管を詰まらせる原因になります。
(搬送パイプ専用イオナイザ EI RIF をみる)
(除電輪状電極 EI RE をみる)
<グリーンシート>
LTCC用グリーンシートの製造工程では、スラリーというペースト状のグリーンシートの原料を、PETフィルム上にブレードで薄く敷き伸ばして成型します。成型したグリーンシートをフィルムから剥離する工程では、静電気によりシートとフィルムがくっついて、剥離性を悪化させ、歩留まり低下の原因になります。
(スマートイオン(エアフリー パルスDCイオナイザ)をみる)
<パーツフィーダー>
パーツフィーダーで部品を搬送するプロセスでは、ボウルの中の振動しているトラフの上で部品同士が擦れ合うと、部品は静電気を帯びていきます。小さな部品が静電気を帯びると、くっついたり塊になることがあり、詰まりやチョコ停の原因になります。パーツフィーダーの歩留まり低下につながります。 (パーツフィーダーの静電気除去 | 詰まり・チョコ停対策を徹底検証!をみる)
<スクリーン印刷>
被印刷物のフィルム・紙を搬送して印刷機へ入れる工程。フィルム・紙が静電気で ずれたり くっついたりして ライン停止・歩留まり低下・印刷不良を引き起こす。
(スクリーン印刷で樹脂フィルム・紙の静電気対策をみる)
<オフセット印刷・輪転機>
被印刷物のフィルム・紙を搬送して印刷機へ入れる工程。フィルム・紙が静電気で ずれたり くっついたりして ライン停止・歩留まり低下・印刷不良を引き起こす。
(オフセット印刷で紙の静電気対策をみる)
<コンベヤ>
射出成型機で小さな樹脂製品を多本取りして、コンベヤで搬送する。小さな樹脂製品は静電気でコンベヤにくっついてしまい、収集箱に入らない。
(コンベヤで樹脂成型品の静電気対策|くっつき防止・生産性向上をみる)
<スリッター>
スリッターは、フィルム・紙・箔を 丸刃で裁断して所定の幅にする工程です。丸刃で切断する時に、強い静電気が発生します。同時に、切断部からは 切粉・切カスが発生して、静電気でくっついてしまいます。
(最新のエアーフリー除電技術でスリッターの静電気対策をみる)
(スリットカスを除去する3つの方法|切粉の問題はこれで解決!をみる)
<充填・製袋>
充填・製袋工程は、粉体やペレット状の製品を、袋・容器に入れる工程です。静電気で粉が容器の入り口に付着して、容器の底へ落ちない問題があります。
(充填・製袋工程で静電気対策|粉・ペレットの詰まり防止をみる)
<縦型包装機>
縦型包装機は、充填・製袋包装機の一種です。袋にするフィルムをガイドロールを介して搬送し、袋状にするプロセスで、静電気が発生して、フィルムがくっつく・しわになる・袋の「口」に粉がくっついてしまし、シール不良になる 問題があります。
(縦型包装機の静電気対策をみる)
<クリーンルーム>
室内に浮遊している微細なパーティクル・ホコリ・微粒子。静電気を帯びると、ワークピースに引き寄せられ、付着することがあります。
(エアーフリー除電技術でクリーンルームの静電気対策をみる)。
c) 静電気放電・スパークの問題→事例と対策
人体を通して放電:
人体を通して静電気放電が生じても、ほとんどの場合 人体に危険が及ぶことはありませんが、身体的な不快感や、放電のショックで身体を機械にぶつける等の事故につながる恐れがあります。
<フィルム巻取り・巻き出し>フィルム巻取り工程では、静電気を帯びたフィルムをコイラーで巻き取っていくことで、ロールは静電気を蓄積して強く帯電します。フィルムの材質により、冬場は静電気が数十kVに達することもあります。ロールを取付け・取外しを行う作業者にとって、「バチッ!」とくる放電は不快です。作業環境の悪化につながります。
(巻取りロールの静電気を効率よく除電する方法をみる)
(巻き出しロールの静電気を効率良く除電する方法をみる)
<スライサー>カーシートやマットレスには、ウレタン材料が使われています。用途に応じて、高反発・低反発なスポンジを加工・制作する作業現場があります。スポンジのような発泡製品の加工現場では、弾力性が高い基材を切断するために、スライサーという特別な加工機でスライスします。スライスする時に砥石と発泡体の間で静電気が発生します。スライスした後、作業者が手作業で積み重ねていく工程では、「バチッ!」と静電気放電を体感します。作業環境の悪化させる原因になります。
(スマートイオン(エアフリー パルスDCイオナイザ)をみる)
<静電気破壊>
半導体デバイスの生産工程では微弱な静電気放電でも回路を破壊することがあります。
(高周波ACイオナイザで静電気対策をみる)
|| 静電気を制御して、生産を効率化させているプロセスもあります
<材料分別>
原料のリサイクル等で使用するドラム型セパレータで、異種の原料を分別するために帯電バーを使用する用途があります。
(静電気で異種の原料を分別する方法をみる)
<フィルム・紙 蛇行防止>
ロールトゥロールプロセスでウェブ(フィルム・紙)の位置決めの用途です。ワインダーで巻き取る直前の金属性ロール上で、フィルム・紙の端面を帯電装置で帯電させて、ウェブをガイド上で静電気で密着させます。これにより走行しているウェブが横方向へずれるのを防ぎ、きれいに巻き取ることが出来ます。キャストフィルムの製造ラインでは、冷却ロール状でフィルムが巻き込むのを防ぐために、フィルムの端面を帯電装置で帯電させて密着させて巻き込みを防止します。
(帯電装置でフィルムの蛇行防止をみる)
<ターレット巻取り機>
帯電装置には、メタルの巻き芯コアへフィルムや紙を静電気で定着させる使い方があります。帯電バーを取り付けて、フィルム・紙を新しいコアへ貼り付けする作業を自動化する使い方です。
(ターレット巻取り機でフィルム巻付け作業を自動化する方法をみる)
<貼り合わせ>
ガラスとフィルムを静電気の引力を利用して、貼り合わせる用途があります。
(静電気で保護フィルムをガラスに定着させる方法をみる)
<粉体静電塗装>
粉体静電塗装では、帯電した塗料をアースした非塗装物に噴霧することで塗装する技術。塗料粒子をマイナスに帯電させて噴霧する場合、アースした非塗装物は静電誘導により表面に逆の極性の電荷(プラス)が表面に誘導されます。これにより非塗装物表面のプラスと塗料粒子のマイナスが引き合い塗着することが出来ます。
<タルク塗布装置>
電線製造工程では、タルク(石灰)を線に塗布するプロセスがあります。この機械をタルクマシン・タルク塗布装置といいます。タルクは、鉱石を細かく粉砕した無機粉末です。タルクを電線表面に塗布して、その後工程で、タルクの上からインシュレーション(絶縁層)を被覆します。タルクの役割は、剥離性の向上です。電線を使用する現場では、電線の端末加工する時に、不要な絶縁層をはがして使います。タルクが塗布されていることで、電線のインシュレーションをはがしやすくする効果があります。電線製造工程では、タルク塗布装置は、タルクを充填したボックスを線が走行することで、全周にタルクを塗布させていきます。電線全周にきれいに塗布させるためには、ボックスを通過する前に帯電装置を設置して、電線表面に静電気を付与する方法があります。これにより、タルクは静電気を帯びた電線全周にきれいに密着していきます。
|| 粉塵爆発と爆発性粉塵
粉塵爆発の3要素は、①可燃性の粉塵、②酸素、③着火源 です。
可燃性の粉塵には、亜鉛・コバルト・ニッケル・アルミニウム・マグネシウム・チタン・小麦粉、などがあります。そして、静電気は着火源になりえます。
|| 危険区域での放電
揮発性有機溶媒や爆発性粉塵を取り扱う区域では、静電気放電は必ず避ける必要があります。
例1)自動車部品製造工場で、塗装工程のブース内では、有機溶媒が揮発して空気中に拡散していることがあります。このようなブース内で、自己放電型または電圧印加型の除電器を設置すると、スパークして印加する可能性があり、重大な事故につながる恐れがあります。
例2)フィルム印刷工場で、グラビア印刷機の周辺は、有機溶媒が揮発して空気中に拡散していることがあります。印刷機周辺には自己放電型または電圧印加型の除電器を設置すると、スパークして印加する可能性があり、重大な事故につながる恐れがあります。
|| 産業用途での静電気除去・除塵について
〇 異物や微粒子による問題
工場で発塵するダストは、設備から機械的に発塵する物だけではありません。ダスト・繊維くず・パーティクルは生産環境中に漂っている浮遊塵埃もあれば、作業者から発塵する毛髪・カス、搬送プロセス・包装プロセスで製品に転写する異物もあります。このような付着異物は製品の不良率を上昇させる可能性があり、その分 余分なコスト上昇につながります。製品の清浄度や品質保証に対する強い要求に応えるため、汚染源の調査や分析作業が必要になります。
〇 汚染の種類
発塵元で分類
□ 製造プロセス(充填、切削カス、磨耗屑、など)
□ 設備(磨耗屑など)
□ 添加剤(離型剤、潤滑剤など)
□ 環境(ゴミ、ホコリ、すす、粉など)
□ 人員(毛髪、繊維屑、指紋など)
□ 包装(磨耗屑、繊維屑など)
〇 原料で分類
□ 有機物・無機物
□ 金属・鉱物・セラミック・プラスチック・天然物質
□ グリス・油
〇 集合状態で分類
□ 固体
□ 液体
□ 接着物・ペースト
〇 化学的・物理的性質で分類
□ 力学的性質(磨耗性、滑り性、接着性など)
□ 化学的性質(極性、非極性、有機物/無機物、分子など)
□ 電気的性質(静電気、電荷を帯びる、磁化を帯びる、など)
□ 熱的性質(膨張率、温度安定性、など)
□ 粘性(表面張力、接着力など)
□ 気体の性質、液体の性質(粒子サイズ、接触面など)
〇 パーティクルを分類
□ コランダム(酸化アルミの結晶)
□ 金属粒子
□ 非鉄金属粒子
□ 繊維
□ けば
|| 生産環境での異物の量
量の問題として、クレーム;不良率;不良により発生する余分なコストなどがあります。これらは、実際の生産中に明らかになることが多く、原因は生産プロセス中にあるケースもあります。
汚染源は多様です:
部材の清浄度が不十分だったり、部材に削りカス・はがれカス・切れ端が付着していることに起因していることもあります。対策として、前洗浄・加工時に洗浄・後洗浄する施策があります。ドクターエシャリッヒは、このような用途に適した装置化された除塵装置を供給しております。
〇 落下する粒子
粒子径50μm~1mmのパーティクルは、裸眼でみることが出来ると言われています。例えば、重工業の現場での工場ダスト、毛髪、粉、繊維屑などがあり、これらは粗大粒子といいます。50μm~0.1μmのパーティクルは顕微鏡で観察することができます。バクテリア、塗料の顔料成分などがあり、微粒子といいます。粒子のサイズは、集塵機のフィルター選定に重要な要素です。
〇 浮遊する粒子
粒子径1μm以下の粒子は、生産環境中で落下せずに浮遊し続けています。気管から肺に進入するので呼吸性粉塵ともいいます。これらの中には、微小なすすや金属カスも含まれています。粒子径0.1μm~10μmの粒子は、捕集できる集塵機用フィルターがあります。
〇 最も小さな粒子
粒子径0.1μm以下になると、電子顕微鏡でなければ検出することは出来ません。極めて小さな浮遊微粒子やエアロゾルは、サイズ0.01μm~0.1μmです。捕集するためには、HEPAフィルター・ULPAフィルターを使用します。0.01μm以下の粒子は活性炭フィルターで部分的に捕集することが出来ます。
|| 除電器・イオナイザの種類と選び方
製造現場の静電気対策は、大きく5つに分類できます。
A)電圧印加型 除電器
B)自己放電型 除電製品
C)放射線による除電方法
D)静電気除去液
E)湿度管理
(参照:静電気を除去する方法 でも詳しく取り上げています)
その中で、(A)電圧印加型と(B)自己放電型には、次のような静電気対策商品があります。
<電圧印加型>
◆ACイオナイザ
◆パルスACイオナイザ
◆高周波ACイオナイザ
◆パルスDCイオナイザ
<自己放電型>
◆除電紐
◆除電ブラシ
これらを分類して整理した新しいサイトを作りました。
用途に適した静電気対策製品を選定する ヒント にご参照ください。
除電器・イオナイザの種類と選び方|4つのポイントで早わかり!をみる
関 連 情 報
ドライクリーナー・洗浄装置の種類と選び方をみる
なぜゴミや異物の問題がなくならないのかをみる
NEW! エアーフリー除電技術がカーボンニュートラルに貢献できる理由
NEW! エアーフリー除電技術は工場のSDGsへの取り組みの切り札!